KOCKUMS KT SERIES
Dense phase conveying system
Available in
Asia, Canada & USA, Latin America and OceaniaThe KT Series Dense Phase Pneumatic Conveying Systems are the foundation of Kockums' conveying equipment. They have undergone continual development to form today's comprehensive range.
They are ideally suited to convey fine fluidizable powders over distances from 5m to a kilometer and throughputs of up to several hundred tonnes per hour.
Dense Phase Conveying systems are normally configured with a conveying vessel under a silo or feed system and connected to one or more destinations via a conveying pipeline.
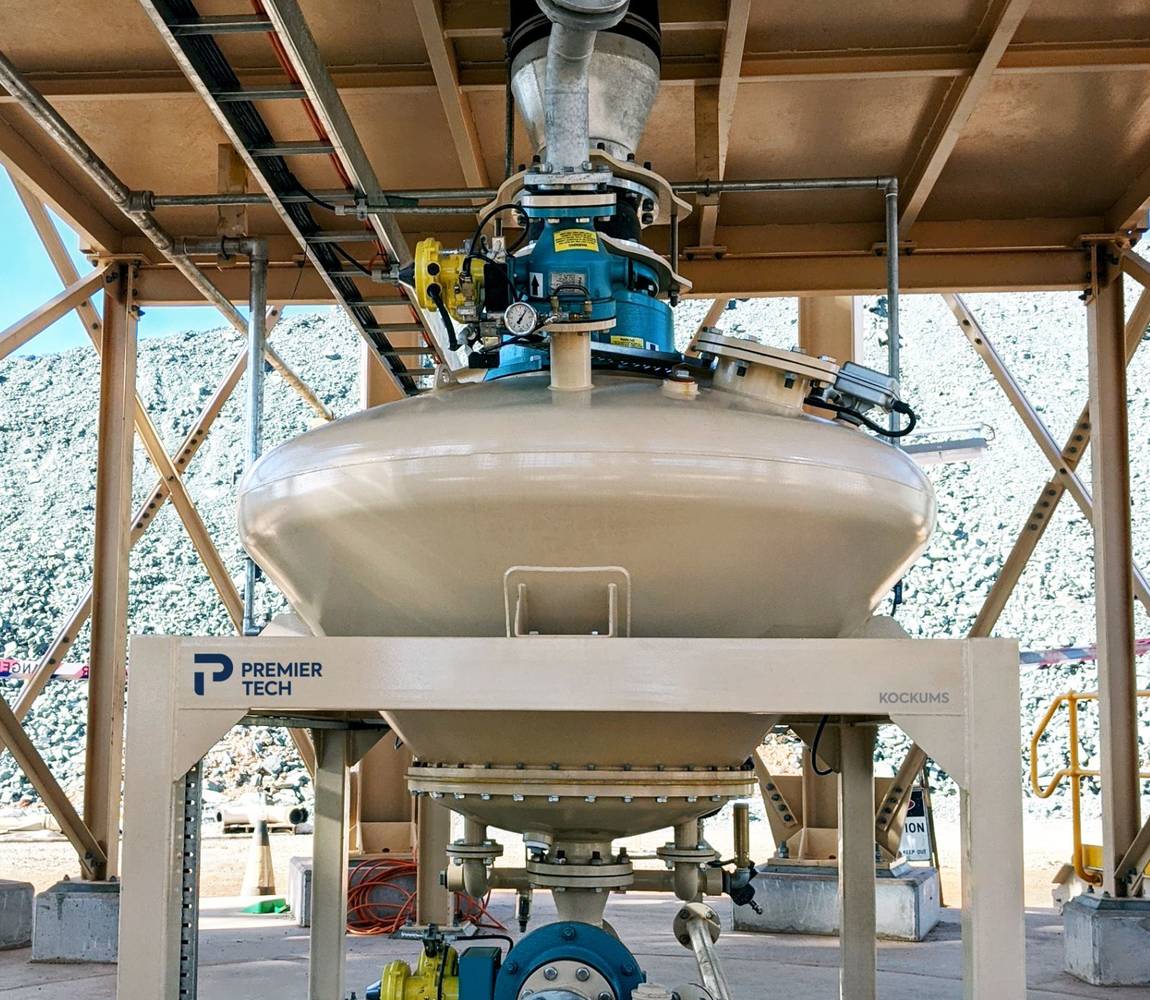
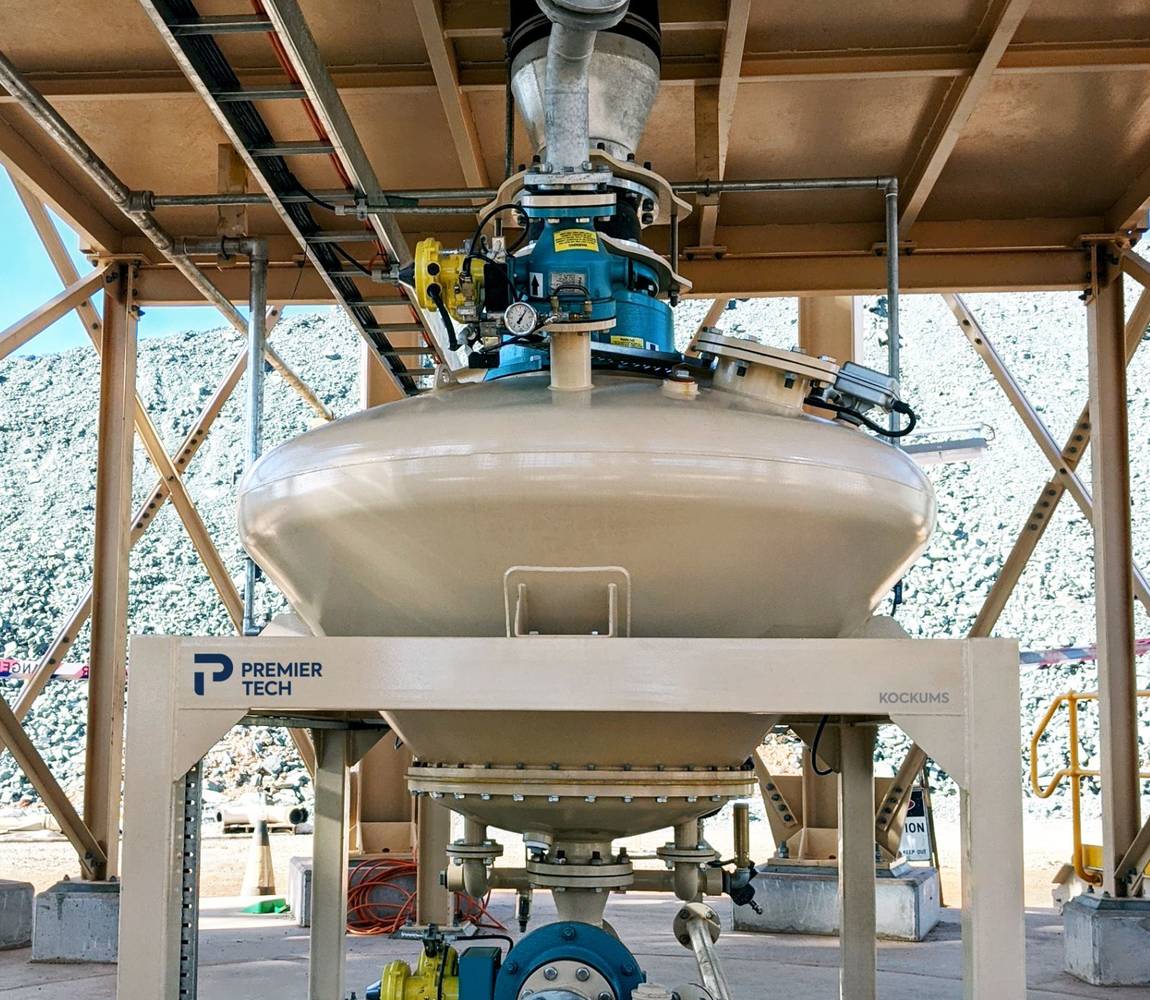
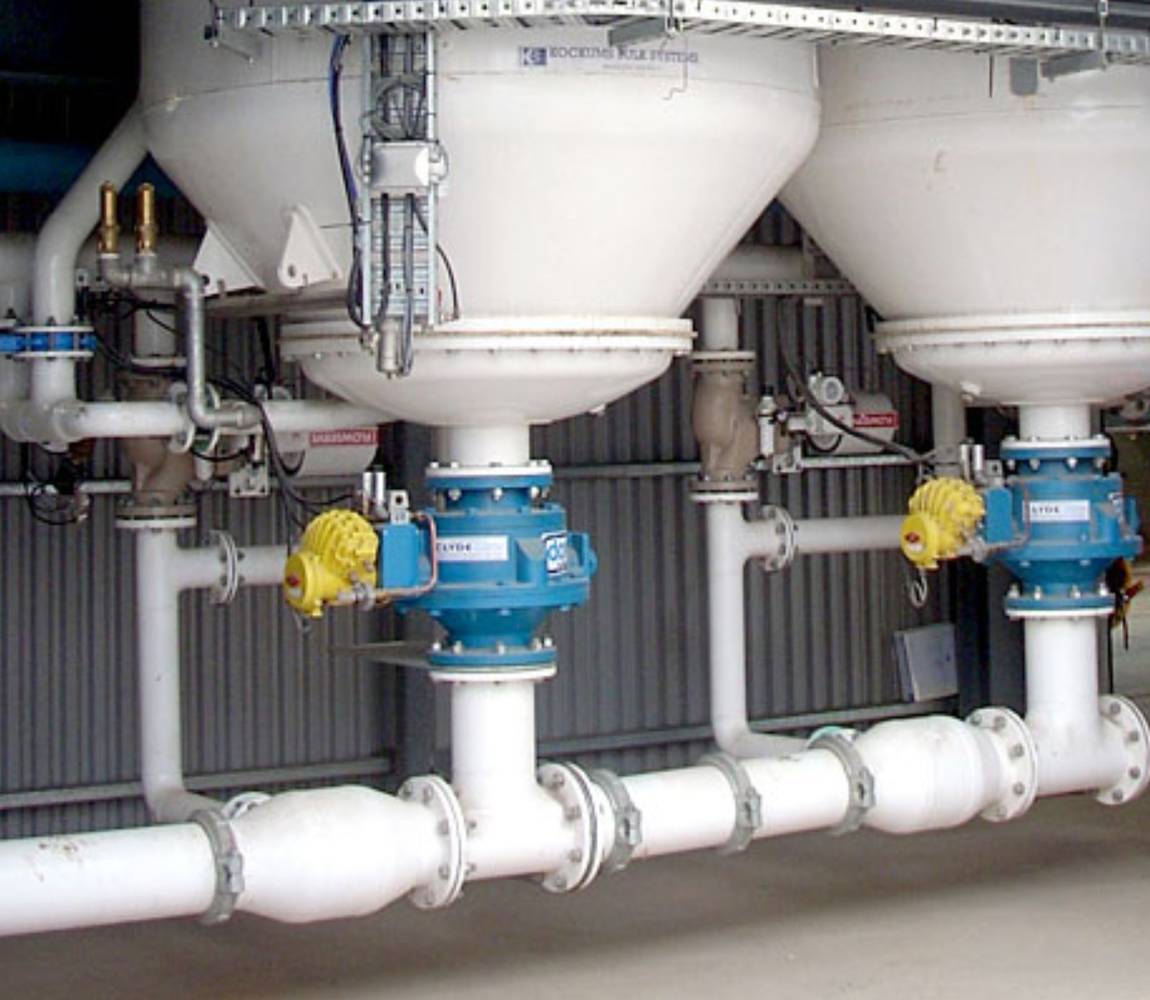
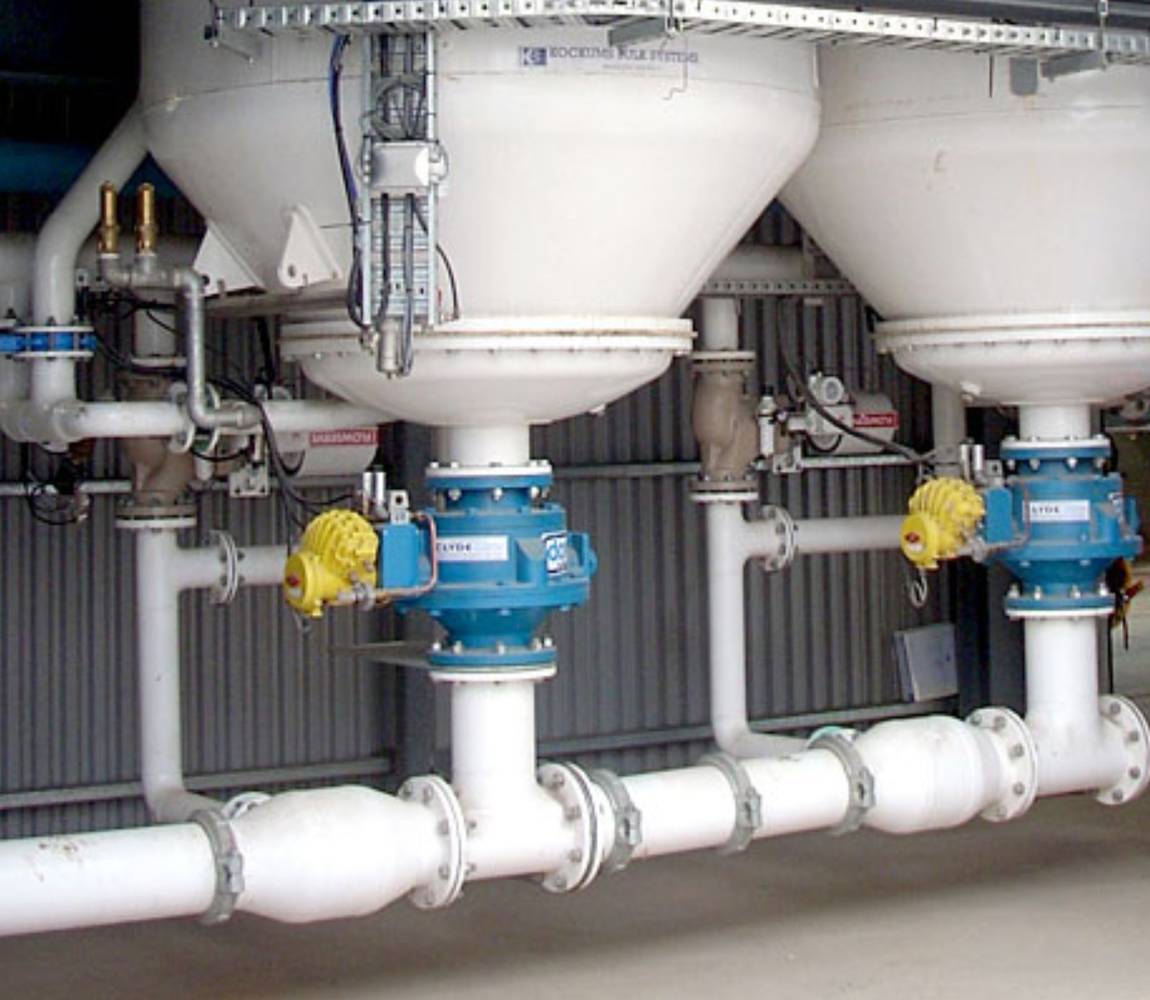
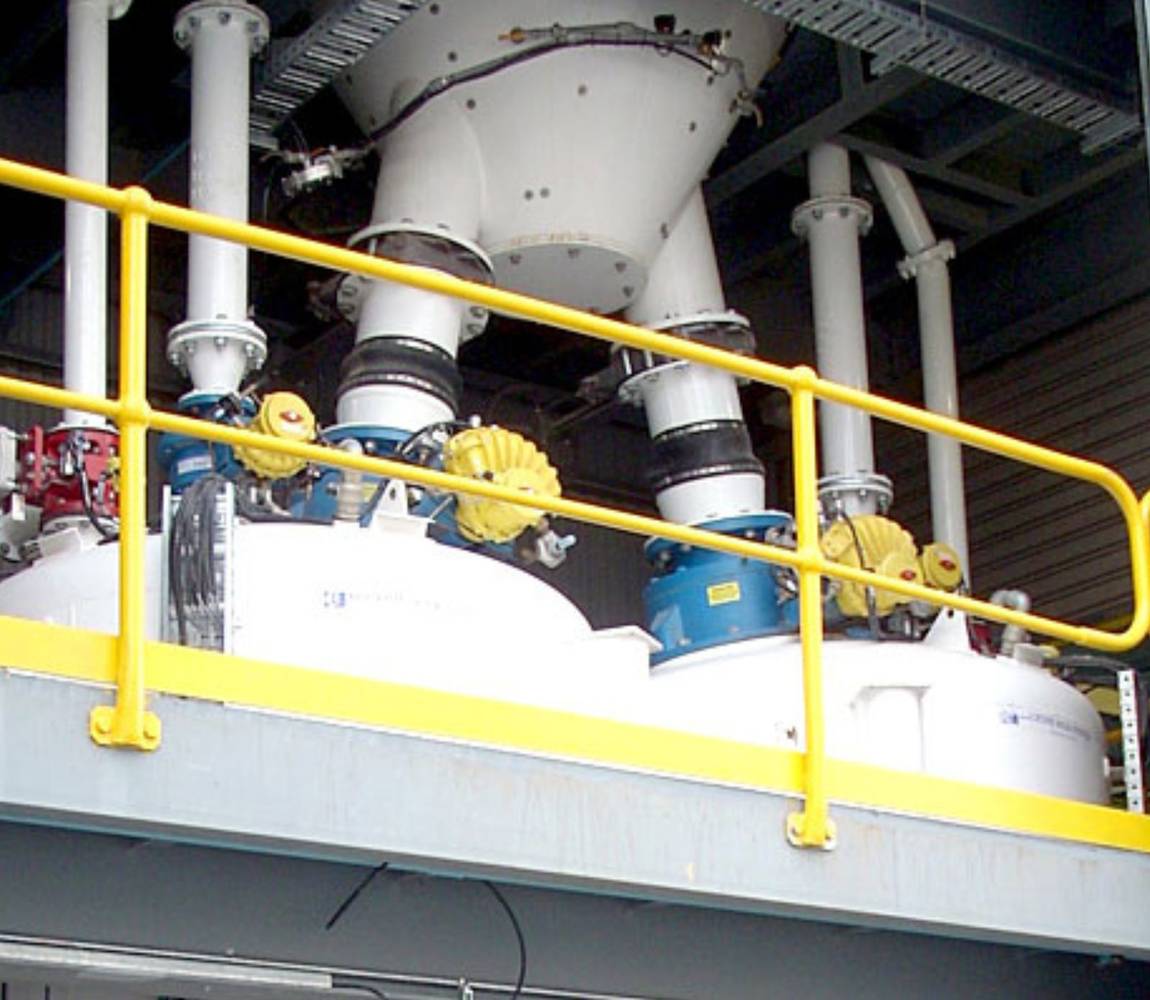
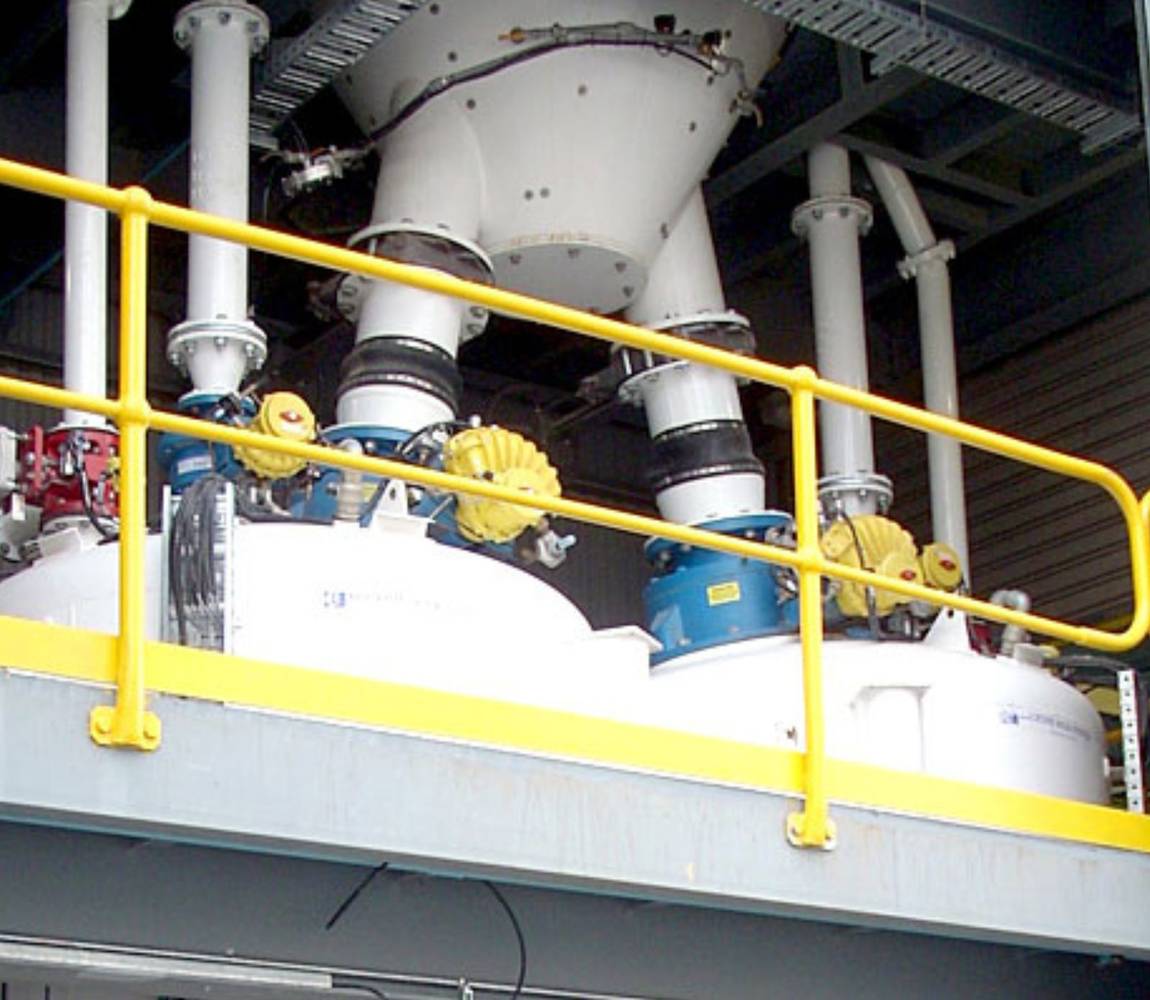
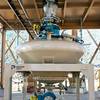
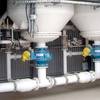
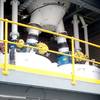
How they work
Each destination must be suitably equipped to receive the material. A compressed air source is required to provide the conveying motive air, either from a blower or plant air.
The conveyor is filled via the top inlet valve, normally under gravity conditions. Once full, all valves are closed, and the conveyor is pressurised. When the kick-off pressure is reached, the discharge valve is opened, and the material transfer begins.
About dense phase conveying
This mode of conveying, “Dense Phase”, minimises the air usage required to move large quantities of powder by maintaining high conveying mass ratios. This means smaller pipelines can be utilised, and smaller pipes require less conveying air, and this has a direct impact on power costs. Dense Phase is the most efficient mode of pneumatic conveying.
Further efficiencies can be gained by use of a twin vessel continuous conveying system which always maintains a full conveying pipeline. This is ideal for longer conveying distances.
Dense phase also has the lowest conveying velocities of all pneumatic conveying systems, which is why it is the first choice when handling abrasive materials. The low velocities keep system wear to a minimum, and where applicable, keeps material attrition negligible.
Applications
From silos, bulk bags or mixers feeding into destination silos that often feed the downstream packaging lines.
Bulk materials
Common materials handled: cement, fly ash, bentonite, gypsum, lime, magnesium oxide, barites, carbon black, calcite, plaster, sand, soda ash, sugar, stearic acid, limestone, calcium carbonate, roasted coffee beans, pvc powder, flour, maize grits, rice, flocculants, and many others.
Rates: up to 200 tonnes per hour
Distances: 5 to 1000 meters
Bulk materials: powders
Features
Performance
- Offers the highest efficiency of all types of pneumatic conveying
- Equipped with fast-acting posiflate inflatable seat butterfly valves for reliable and rapid shut-off
Heavy-duty design
- Rugged design for heavy-duty applications and environments, such as mining, power, and cement industries
- Includes robust and wear-resistant dome valves designed for abrasive materials
- Operates at low velocities to minimize system wear and material attrition
Versatility
- Small-bore pipelines allow for greater flexibility in transferring powder through congested plants
- Suitable for both batch and continuous conveying processes
Options
- Compliance with AS1210, ASME and PED
- High temperature upgrades
- Blower packs
- Weigh system
- Wide variety of pipe, bends, and diverter valve options