YEAR ONE Program
Installing a new machine is no easy task! This is why we offer immediate and direct support during the critical first year of operation to ensure a successful installation.
To do so, we've combined field service visits, training and parts solutions to ensure the first year of operation runs as smoothly as possible.
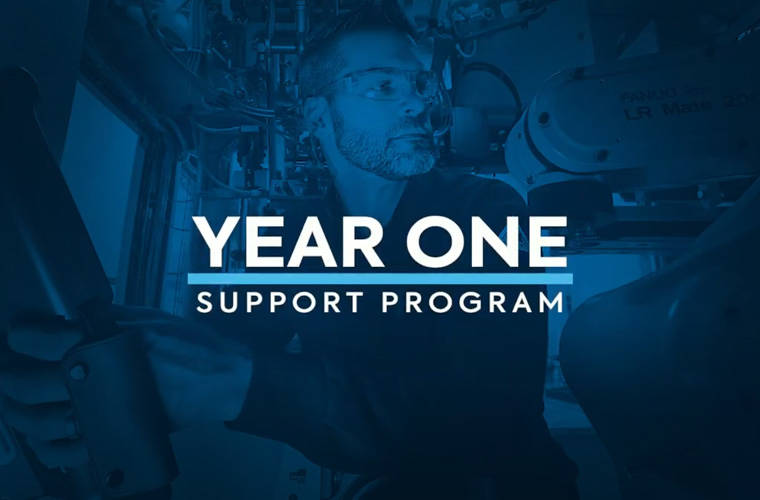
The program consists of three visits set at critical milestones during this time, each with a set task list. The YEAR ONE support program will help your team understand the technical nuances of your equipment and ensure your put forth the best maintenance habits from the start.
Maximum productivity and reliability from the very beginning of any new installation
1st Visit
One month post installation
Visits details
Your equipment is up and running, and your team members are becoming familiar with its operation and components. It is likely that your operators and maintenance personnel will experience a dip or plateau in their learning curve as they begin to know and work with the equipment. This will in turn result in a fluctuation in your production rates. The equipment will also need regular upkeep and begin to require preventive maintenance.
Visit tasklist:
✓ Equipment operation training and education about best practices
✓ Equipment tuning and optimization
✓ Maintenance follow-up and training
✓ Spare parts inventory review and recommendations
✓ Technical support contact information review
2nd Visit
Six months post installation
Your equipment has now been running for a little while longer, and operations are running more smoothly. Your team members have accustomed themselves with the new automated processes and are ready to further their skills and knowledge of the equipment. You may also have new operators that need training.
Visit tasklist:
✓ New operator training
✓ Training needs assessment
✓ Complete equipment inspection and tuning
✓ Review of maintenance work done to date and preventive maintenance schedule
✓ Spare parts inventory review and recommendations
✓ Development and/or education on resolution methods of any possible operational issues
✓ Identify and address any warranty-related issues
3rd Visit
Eleven months post installation
Your equipment has now been running for nearly a year, and operations are becoming routine. Your team members have accustomed themselves to the automated processes and have expanded their skills and knowledge of the equipment. It is important to identify next steps moving forward once the warranty is done to ensure your equipment continues to run efficiently for years to come.
Visit tasklist:
✓ New operator training
✓ Development and implementation of solutions for any issues that may have come up
✓ Complete equipment service and inspection with operational status report prior to warranty ending
✓ Preventive maintenance schedule follow-up and review
✓ Spare parts inventory review and recommendations
✓ Review LIFECYCLE Support Program options moving forward after warranty period ends
What you will get out of a YEAR ONE Program
We want to ensure your new equipment is properly up and running, and that your team champions this new investment. Let’s make sure everyone is on the same page and that you make the most of your new production line.
Peace of mind
The YEAR ONE program was specifically designed to provide new equipment owners and those transitioning from manual processes to automation with assistance and guidance throughout the first year of operation of the new equipment – and to consequently remove all the guess work, fear and stress from the process.
Performance
The program focuses on providing you with help and training during the transition period so that you can focus on maximizing performance from the moment your equipment is installed. We ensure your equipment reaches and maintains maximum productivity, and that your team members have the necessary training to operate it and perform the required maintenance.
Cost-efficiency
The program not only ensures that best practices and maximum productivity are attained early on during the transition period, but also helps you avoid simple mistakes and common issues, which can lead to costly breakdowns and subsequent production down time.
Interested in going beyond YEAR ONE?
Premier Tech has many after-sales services to ensure your equipment stays productive and reliable for years to come!