Selecting the Right Case Packer: A Step-By-Step Guide for Manufacturers
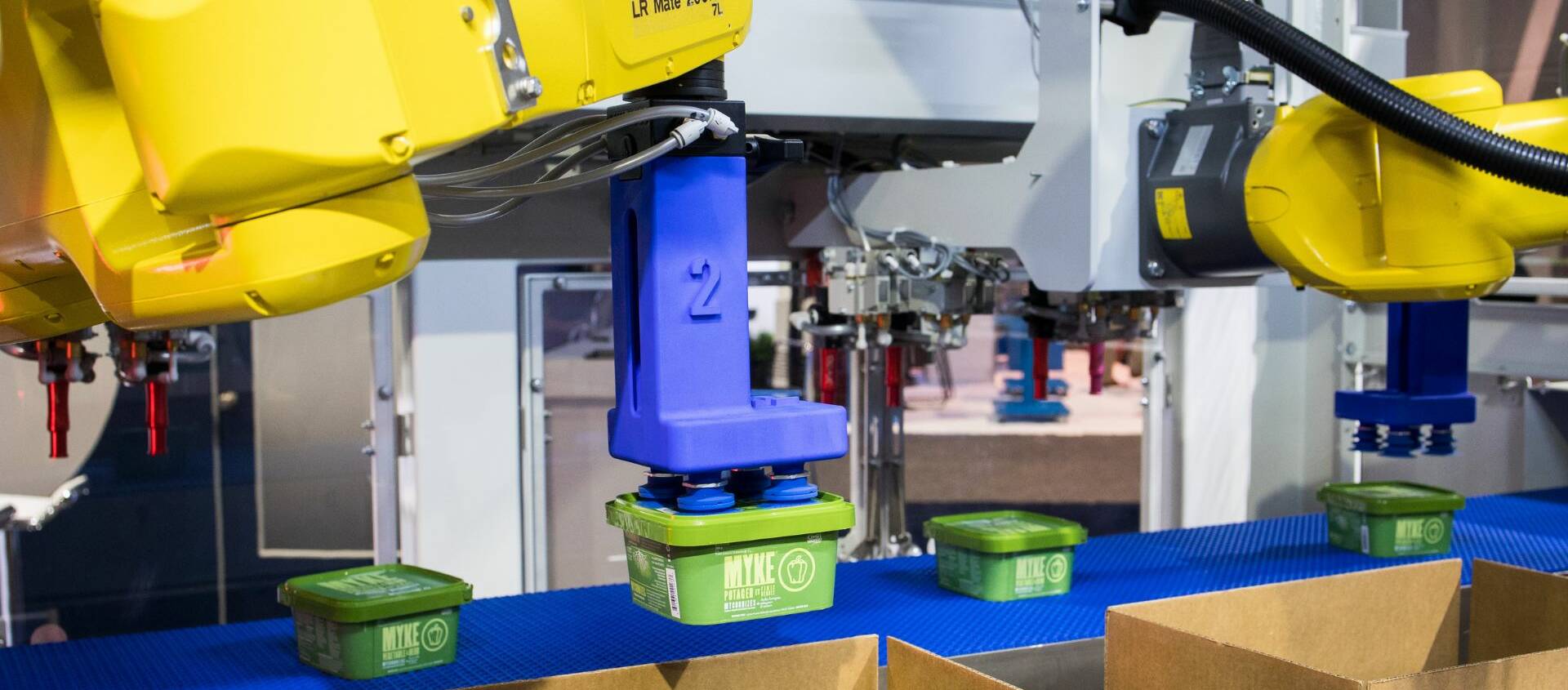
As a manufacturer, you're no stranger to the perks of automated case packing—think faster, more accurate, and safer product handling. Whether you're packing for storage or distribution, automation is sure to streamline your overall process, saving you money while increasing plant safety.
But here's the catch: with so many options on the market, how do you choose the right case packer for your unique operation? In this guide, we'll walk you through everything you need to know to make the best choice for your business.
First, what is case packing?
As a quick refresher, case packing is the process of placing products into cartons or containers. This is an essential part of secondary packaging: the products are already pre-packaged, but they need to be stacked into cases.
Case packing can involve various items, like pouches, bags, boxes, or other types of containers. Cases are optimized for size, weight distribution, and product protection. Case packing ensures that goods can be shipped and stored efficiently, while also meeting retailer or regulatory requirements (such as labeling, display case patterns, or unit counts).
Why is it beneficial to automate case packing?
Choosing to automate the case packing process can translate into numerous benefits, including:
Faster packing speed
Automated case packers can move much more quickly than manual workers, vastly increasing throughput. Not to mention machines can run 24/7 with minimal downtime for maintenance.
Improved consistency and accuracy
Automated systems are precise, ensuring consistent placement of items and reducing the errors that are much more frequent with human labor.
Improved safety
Automation eliminates the need for manual handling of heavy cases. By automating repetitive, physically demanding tasks, automated case packing machines reduce accidents and injuries.
Quality control
Automated systems often use sensors or cameras to ensure accuracy of packing. Plus, automated systems often come ready to handle items gently, reducing the risk of mishandling or damage.
How do I get started with choosing a case packer?
A key starting point is understanding that case packers generally fall into two main categories: mechanical case packers and robotic case packers.
Traditional case packers
Traditional mechanical case packers are typically fast, high-throughput systems designed for repetitive tasks. They are generally less flexible, but ideal for high-volume production of consistent products with minimal variation.
Robotic case packers
On the other hand, robotic case packers are highly flexible and can handle a wide variety of products, sizes, and packaging formats with quick changeovers. In this category, there are three common configurations:
Wrap-around case packers
Wrap-around case packers are an economical, all-in-one solution. They erect cases from flat pieces of corrugated cardboard, pack products inside, and securely close them. This process not only reduces packaging costs by using less cardboard, but also reduces shipping costs as the process packs products more tightly into cases.
Top-load case packers
Top-load case packers, such as the CHRONOS CPD Series or CPC Series, place products into cases from the top, and arrange them horizontally or vertically in the container. Highly versatile and modular, these kinds of case packers are great for high-speed production environments.
Side-load case packers
Side-load case packers are great for irregularly shaped or delicate items. They erect corrugated cardboard cases before gently pushing items into the cases laterally, minimizing the risk of damage or shocks that can compromise your products.
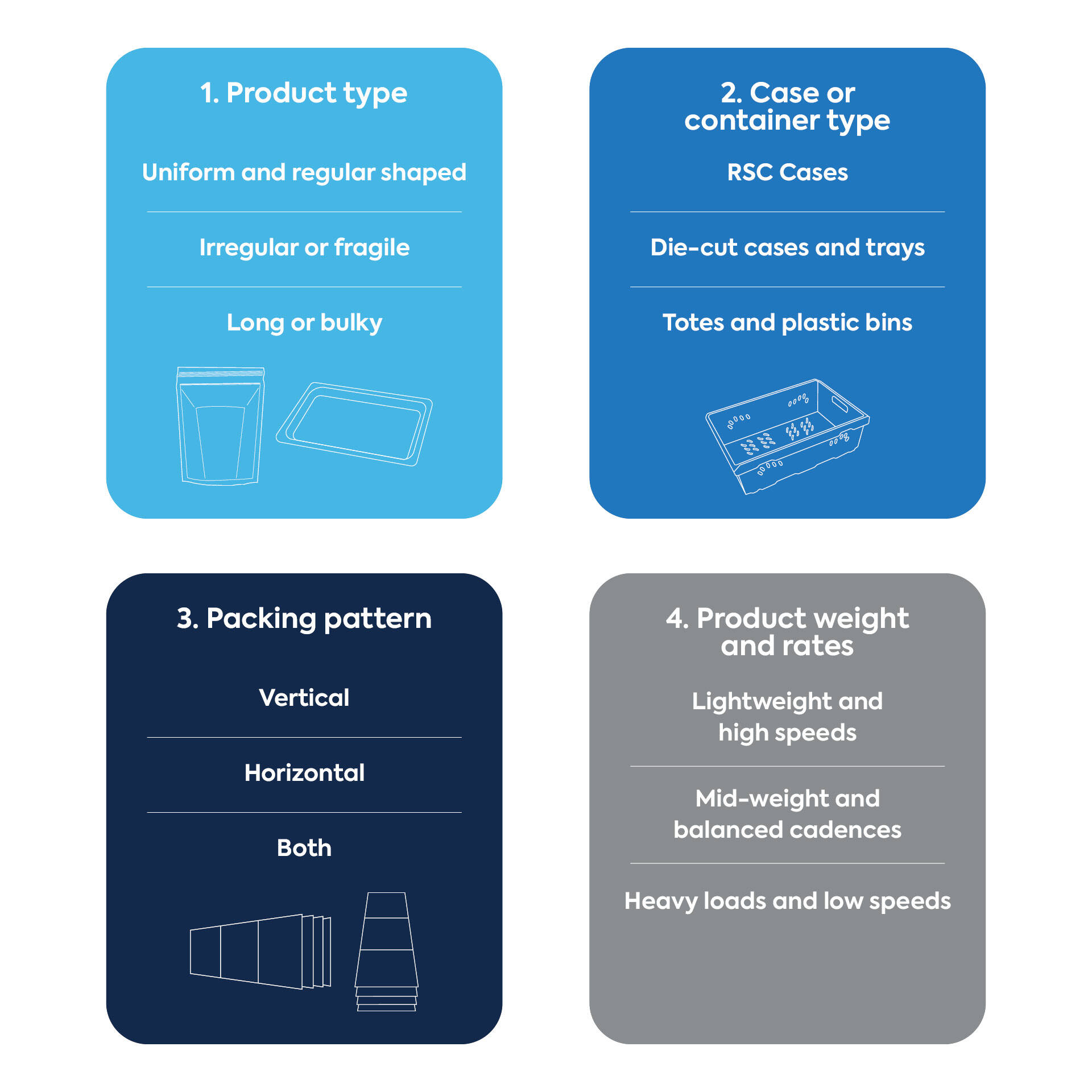
1. Product type
The kind of product you handle will inform the type of equipment you choose:
- Uniform, regular-shaped products (e.g., cans of soda, bottles of juice) are equally suited to a mechanical or robotic set-up, though the mechanical will offer higher speeds.
- Irregular or fragile products, such as glass jars, lidded cheese packs, or trays with plastic on top are well suited for a top-load case packer or wrap-around case packer. Such products benefit from precision and gentle handling, as they are placed carefully into cases with the risk of crushing or damage.
- Long or bulky products, such as personal hygiene products, will be a good match with a side-load case packer. These systems can easily handle bulkier items, placing them into cases from the side, without compromising on layout or efficiency.
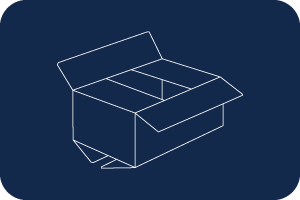
Regular slotted containers (RSCs)
The most common type of packaging in North America for consumer goods. They can be handled by mechanical, top-load, and side-load case packers.
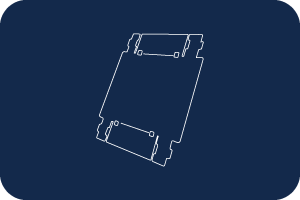
Die-cut cases and trays
Another popular choice are cases and trays made from flat cardboard blanks (die-cut). A wrap-around case packer is used to form the blank into a sturdy shape that suits your product.
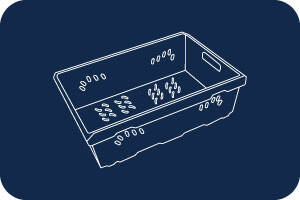
Totes and plastic bins
Often used for meat or protein products, or personal care items, these containers best suit for top-load case packers.
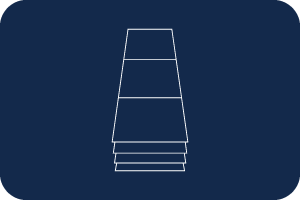
Horizontal
Top-load and wrap-around case packers are ideal.
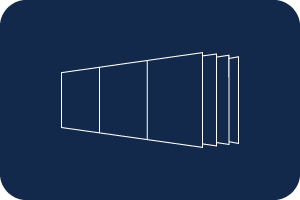
Vertical
Side-load, wrap-around and some top-load case packers suit vertical patterns.
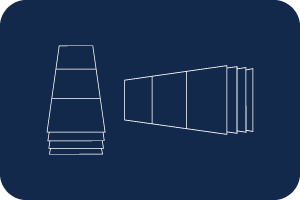
Both
Top-load and wrap-around case packers can do both horizontal and vertical packing.
4. Product weight and packing rates
Finally, the weight of your products and their associated packing rates will determine the type and number of robots required in your case packing machine.
Typically, lightweight products will be packed at higher speeds, while heavy loads will be handled at slower rates. Your case packer manufacturer will provide guidance to ensure you have the right equipment based on your specific product list.
An automatic case erector creates square, structurally sound cases, which ultimately pack better, stack better, and protect better. They provide the structural integrity needed for optimal storage and shipping.
A case sealer is a machine that can securely seal the top and bottom flaps of an erected corrugated cardboard box with tape or glue. In this way, case sealers can maintain the integrity of the package and ensure the packed products remain secure.
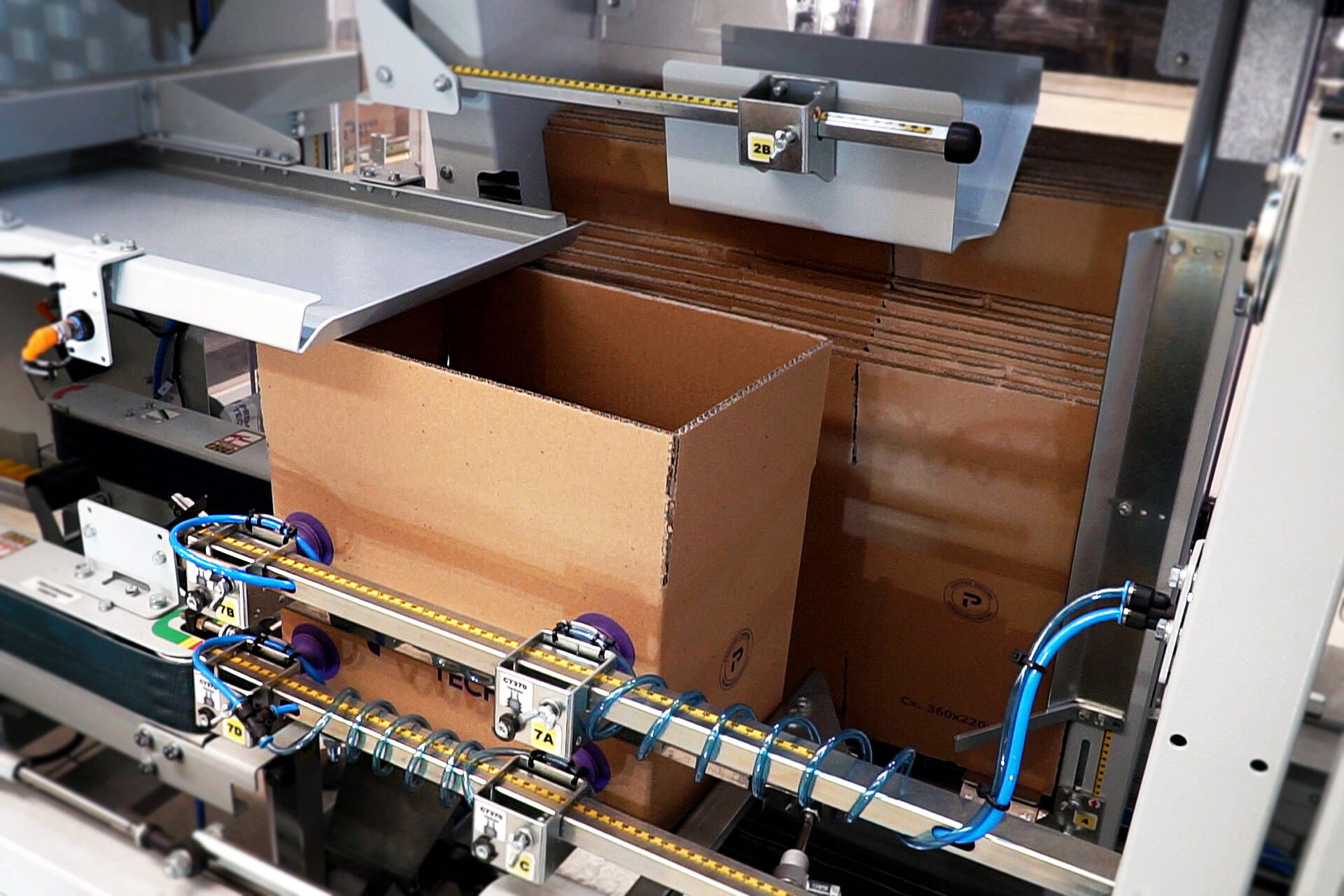
Maximize efficiency with the right case packer
As manufacturers grapple with increasing demands, automated case packing has become essential. Choosing the right equipment is key for maximizing the benefits of speed, consistency, safety and quality control. With our guide, you'll be able to choose the ideal case packing system from a trusted manufacturer that best suits your needs.
Ready to automate your end-of-line equipment?
Take a look at Premier Tech’s expanded portfolio of case packers with extended options for your packaging operations.