From Powder to Package: A Guide to Choosing the Best Bagging Machine for Your Powdery Food Ingredients
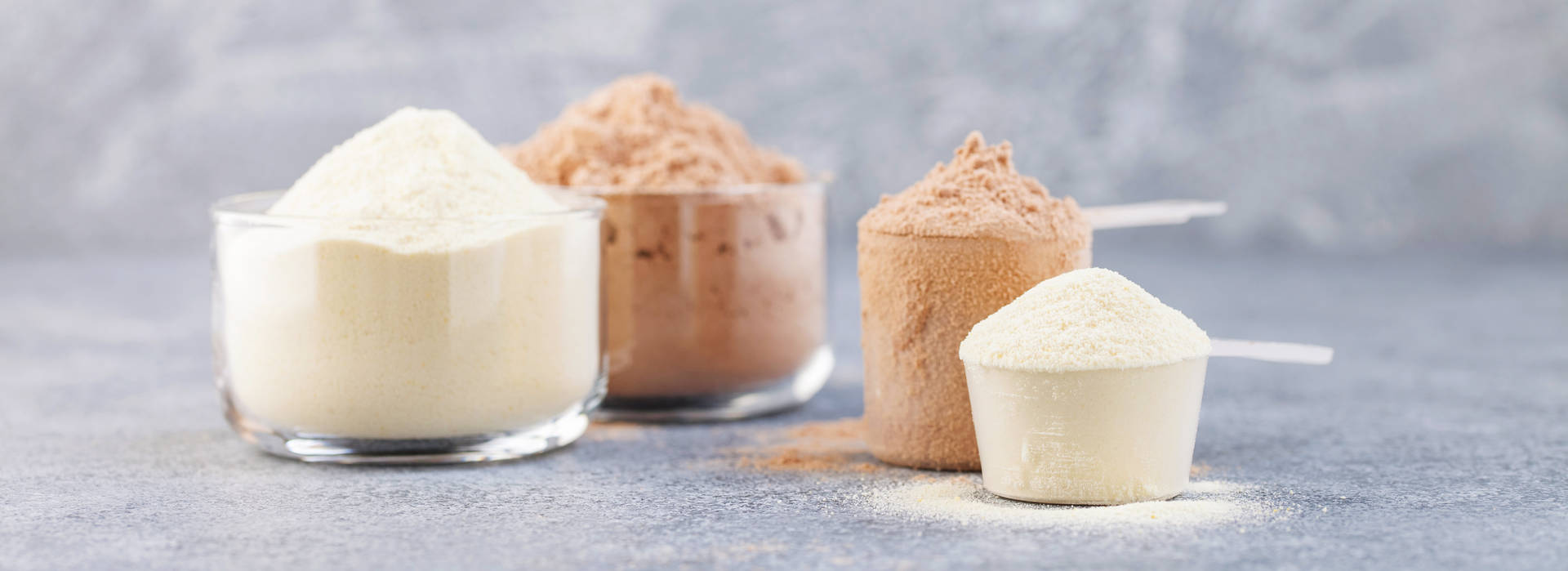
Food safety is a critical aspect of food production. Whether it’s fresh, raw ingredients or ready-made meals, it’s imperative that manufacturers pay close attention to every single step of the production line, and one of the most important steps is a hygienic bagging system.
By carefully selecting the right bagging equipment, manufacturers can ensure that their products are properly contained and protected, helping not only to safeguard the reputation of their brand, but the health of their customers.
Why powdery foods require ultra-hygienic bagging systems
One category of food product that requires an extremely hygienic process and clean bagging machines is powdery food ingredients - think milk powder, non-dairy creamer, whey powder, seasoning powder, bakery mixes, flour, and food supplements.
These powdery bulk materials must be sterilized and evaporated to increase their shelf life. If food safety is neglected, there are risks of:
- Biological hazards (from microorganisms)
- Chemical hazards (contaminants from raw materials or machines)
- Physical hazards (from extraneous materials) Unintended chemical reactions (from product aeration)
- Cross-contamination (on the same line there could be multiple products that contain allergens such as gluten, milk products, or eggs)
Furthermore, products like food formulas for babies and elderly people require much higher sanitary standards than other powdery food ingredients.
5 Factors to consider when choosing a bagger for powdery food ingredients
If you’re looking for an automatic bagging machine for your powdery bulk production, here are five things you should consider before making a purchase:
- Sterilized equipment with minimal residuals
- High-quality de-aeration system
- A design that prevents contamination
- High cleanability
- Food grade lubricants and machine components
Let’s break these down.
1. Sterile equipment with minimal residuals
It is unavoidable that a bagging machine encounters powdered products during the packaging process. Thus, there is a risk of chemical contamination, as well as a potential chemical reaction between the powder and the metal parts of the machine.
Bagging machine parts that come into contact with the product should be made of food grade stainless steel that is highly polished, making it resistant to rust and corrosion from acid, alkaline, and chloride.
Further, the bagging machine should be designed to have minimum contact with food ingredients to ensure no powdery remnants remain inside the machine that could contaminate the next batch.
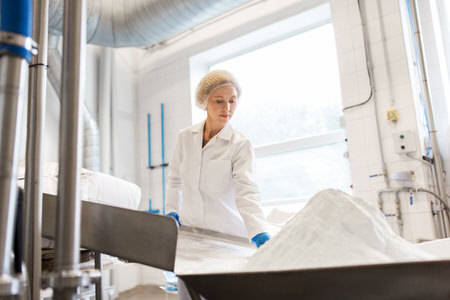
2. High-quality de-aeration system
Powdery food ingredients can be delicate and require specific handling to maintain their quality. So, another factor that manufacturers need to consider is the air inside the product, which can cause oxidation and rapid deterioration. Additionally, if the package contains too much air, the bags can swell and even break.
To address this, a bagging machine with an air suction system, such as a de-aeration system, is essential. Such a system needs to be capable of removing as much air as possible, helping to preserve the quality of the product without compromising its weight accuracy.
With the right bagging machine and air suction system, manufacturers can ensure that their powdery food ingredients are properly handled and packaged to maintain their quality and freshness.
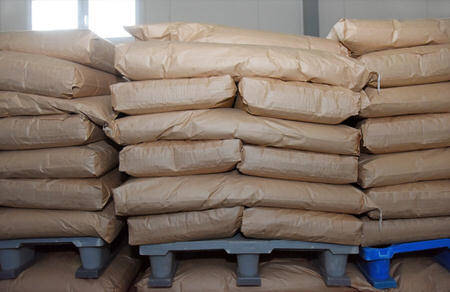
3. A design that prevents contamination
During the packaging process, while the bagging machine is moving the bags from one station to the next, the mouth of the bags remain open. As such, there is a risk of contamination from extraneous materials within the factory.
To reduce this risk, the machine should have:
A sealed cabinet
To prevent contamination from dust or foreign matters, the entire process from filling to closing should be carried out inside the cabinet.
A cover
A cover is an essential tool while the bag is moving from one station to the next for additional safety.
An appropriate bag sealer
To prevent spoilage and contamination and to preserve shelf life, the sealing technology should be able to ensure the bag is tightly closed.
4. High cleanability
The best open mouth baggers for powdery food ingredients need to be designed in accordance with food industry standards. This includes elements like as few flat surfaces as possible to prevent product build-up, and a completely welded structure with no cracks.
A strong design will also feature access points for simple cleaning and the ability to remove critical parts to swap out or clean easily.
5. Food grade lubricants and machine components
Though not every part of a bagger will come directly in contact with your product, ensuring that all lubricants and machine components are food grade eliminates any risk of contamination. This means confirming that everything – from grease to motor oil and conveyor belts to clamps – passes food safety standards.
Additional environmental security
In addition to maintaining the safety standards of the product itself, safety and cleanliness in the workplace is also very important. When looking for a bagging machine, manufacturers benefit from taking note of these additional features:
Dust removal system
The bagging machine should have a dust removal system or be able to connect to a dust collector to minimize dust emissions. This not only reduces risk of cross-contamination and explosion but improves the health and safety of your employees.
Hazard prevention system
The machine should be designed to prevent sparks and explosions. It should be equipped with safety measures that stop it from running immediately if opened, to ensure the safety of operators.
Ready to find the right bagging machine for your powdery food ingredients?
If you’re in the market for an automatic bagging system for your powdery food ingredients, we recommend the CHRONOS BFL Series High-Precision Open-Mouth Bagger from Premier Tech.
This hygienic machine is equipped with a bottom-up filler that’s specifically designed to ensure the safety of your food products. Multiple options, including bag de-aeration, a Clean-In-Place system, and customizable in-feed systems, are available for this model to suit your production needs. Plus, it requires minimal human supervision, saving you valuable time and labor costs.
And that’s not all – we’ve got a team of skilled specialists who can provide quality client solutions including maintenance and after-sales services to all of our customers. Give Premier Tech a try and see how our top-of-the-line bagging machines can help take your food production to the next level.
Get started today
This leading BFL Series bagging machine will allow you to bag powdery food ingredients with the best in safety, hygiene, and overall production line efficiency.