Case Study Moulin Peterschmitt: Staying at the Cutting Edge of Technology
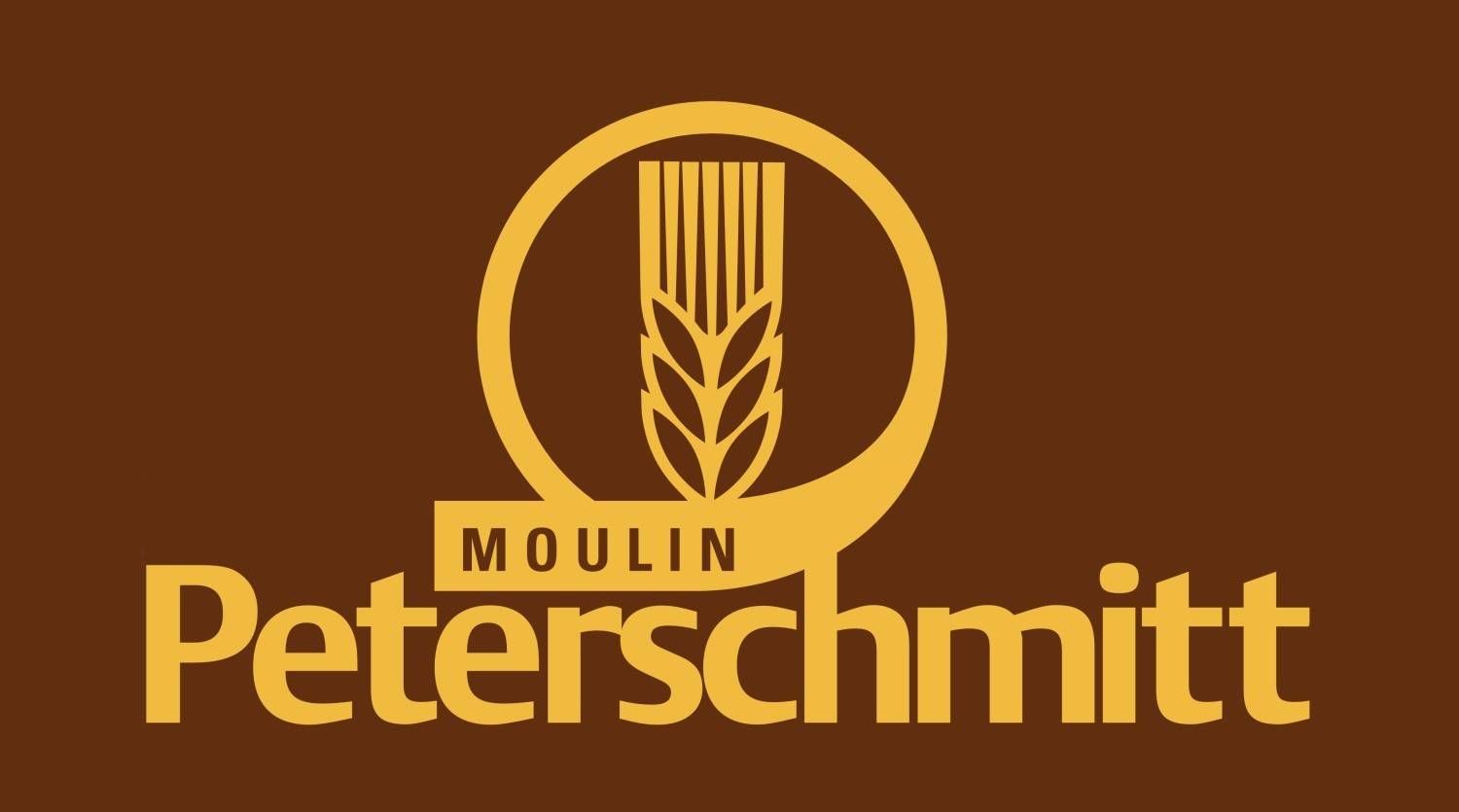
COMPANY PROFILE
Moulin Peterschmitt is a flour mill in the Alsace region of France. Opening in 1782, the mill has been passed down through generations of the Peterschmitt family. Marc Peterschmitt, the company’s president, took over from his father several years ago and runs the mill with brothers Luc and Daniel. They are the seventh generation to manage the mill.
Moulin Peterschmitt produces soft wheat flour on site and has a very large client base, ranging from individuals to industrial companies. The mill therefore sells everything from 1-kg bags to trucks carrying 30 metric (33 imperial) tons of bulk product.
STAYING COMPETITIVE IN THE FLOUR INDUSTRY
Moulin Peterschmitt has continually strived to modernize their line so they can remain competitive in an already highly competitive market. Back in 1782, the company had one mill that crushed around 500 kg of wheat a day. Now, the company produces 5 (5.5) tons of wheat per hour.
However, that’s not enough to stay ahead of the game: the mill wanted to produce more. In addition, the new equipment had to improve sanitation, increase automation, and open up new sales opportunities for Moulin Peterschmitt.
DETAILING THE PLANS FOR NEW EQUIPMENT
Increasing production was the first step in the plan, and Peterschmitt and his brothers had a very clear goal: to double production to 10 (11) tons per hour and also have the option to increase it even further in the future.
To improve sanitation, they found two machines on the market that bagged the sacks at the bottom, which generated very little dust, thereby assisting in maintaining clean facilities. One machine was from Premier Tech and the other, from a competitor.
The bagging machine also had to be automated: “It had to be capable of preparing at least 5 or 6 pallets in advance without anyone having to intervene. For us, it was out of the question to have to keep someone permanently in the immediate vicinity of the machine to make sure everything was working correctly,” Peterschmitt says.
With the old bagging and palletizing equipment, the mill was missing out on one critical sales opportunity: being able to respond to calls for tender for orders in bags. That inability left the door open for competitors to snap up new business.
CHOOSING PREMIER TECH
During Marc Peterschmitt’s grandfather’s time, the company had a Richardson Chronos scale that was used to weigh the wheat at the cereals reception point, back when the farmers delivered directly to the mill. The company then moved to a partially automated machine 12 years ago. “This machine had had its day,” Peterschmitt says, and it was time for a replacement.
Peterschmitt was put in touch with a member of the Premier Tech sales team as soon as he expressed interest in a bagging machine. “And that person has always been very committed and has always answered all our questions, guided me and showed me the different options open to us,” he says.
Moreover, he and his team were able to work closely with the design teams of the various companies involved in the project, including not only Premier Tech but also the manufacturers of the silos and the company selected to reconfigure the building.
In the end, Moulin Peterschmitt chose not only a bagging machine but also a layer palletizer for the bags, because the pallets must travel by truck and therefore needed to meet strict length and width measurements to fill the trucks efficiently.
ACHIEVING THAT SOUGHT-AFTER COMPETITIVE EDGE
Moulin Peterschmitt is a centuries-old company that wants to stay ahead of its time. Upgrading part of its line doubled production, improved sanitation, brought in automation, and opened the doors for new business. “I believe we definitely made the right choice,” says Peterschmitt.