Depalletizing Fundamentals
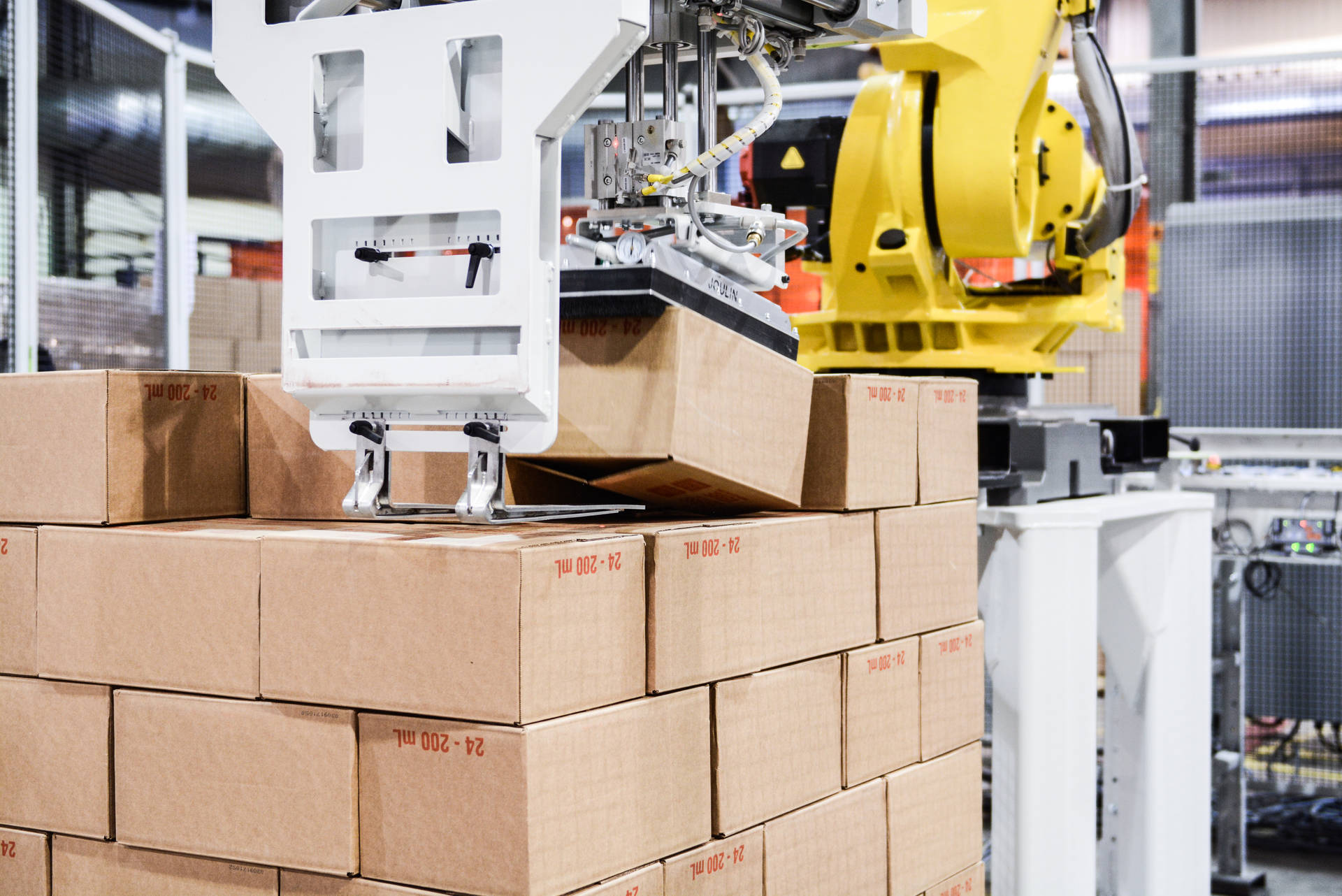
At some point in manufacturing, no matter what product you handle, it’s going to come down to this: Are you being cost-effective? The decision to move forward with automation is usually driven by a desire to boost production rates, improve efficiency, and ultimately, be more profitable. Many companies have already experienced the benefits of robotic palletizing, but when it comes to depalletizing, operations are still often supported by manual labour.
Depalletizing applications are increasingly common in the manufacturing industry. There are various reasons why products need to be taken off a pallet instead of the other way around, and all require different types of arm effectors. Are you depalletizing to another pallet, a conveyor or directly to a transport vehicle? There are as many ways of depalletizing as there are products to depalletize. In the end, you will want your application to be optimal―from precisely locating the product on the pallet, to gently handling it throughout the entire process. The right end-of-arm tool will maximize your operations, and consequently, your ROI and payback.
FUNDAMENTAL KNOWLEDGE
Yes, depalletizing is an art. Some projects require advanced knowledge, and engineers can develop solutions for custom applications.
In the following example for instance, the client requested a depalletizer that would depalletize boxes filled with empty bottles of wine. Specifically, the flaps of the boxes had to be held closed by a custom-designed end-of-arm tool during transport between the pallet and the conveyor.
In applications such as the one shown above, precision is essential. One false move could result in product loss. A Vision System would allow the robot to accurately locate the product on the pallet for a flawless pick.
The right end-of-arm tool plays a decisive role in the success of the application. The tricky part in this particular example was to gently handle the boxes from underneath, since the flaps were not securely closed, and the contents could have fallen on the ground. The end-of-arm tool not only had to pick the case but hold its contents while transporting it. Flexibility was also a concern in this application since the client requested a solution that could handle cases of various sizes. Not only did the gripper have to adjust, but the vacuum tool needed to be customized to handle different products. When a depalletizer is used for various products, the Human Machine Interface (HMI) becomes one of your biggest assets. Quick changeovers between products and/or end-of-arm tools mean more uptime.
No matter the depalletizing solution you choose, and the product you need to handle, always remember to aim for maximum cost-effectiveness with equipment tailored to your industry’s realities. From end effectors to easily configurable HMIs, every part of your depalletizer impacts time spent and money saved.
One of the main challenges in depalletizing, is handling a pallet that hasn’t been properly palletized. If the pallet you receive was manually stacked, chances are the product will not be placed in a picture-perfect square. This type of situation makes it more difficult to detect the precise location of the product and how the arm effector must position itself to accurately pick it up. This is particularly true when depalletizing bags. Their composition makes it hard for them to keep the same shape from one bag to the next. Your Vision System must be adapted to recognize random pallet patterns and unevenly placed products. There are other factors to consider: bag composition, colour and ambient lighting. Is your bag made of plastic, paper or polywoven, for example? The less breathable the bag, the greater chance you have of reliably picking it with a vacuum-type gripper. If your bag lets air leak, then you will have to consider a fork-type gripper for a better grasp. Bags also tend to be more challenging to locate on a pallet. Unlike cases, their dimensions can change depending on how they are positioned. The Vision System will usually locate a logo or significant inscription on the packaging to align the robot for its pick. This is where colours are considered. The greater the contrast between the inscription and the rest of the bag, the easier it will be for the Vision System to accurately identify it.
BUT WHAT CAN AUTOMATION DO THAT WORKERS CAN’T?
Now don’t get it wrong. It’s not that the labour isn’t right for the job, it’s that the production needs eventually surpass their capabilities. Repeatedly unloading products from a pallet is likely to put your labour under a fair amount of stress. Repetitive strain injuries are common among industrial workers and are costly. Loss of productivity, medical leave and insurance costs are just a few examples of the resulting impact. Physical fatigue will have a significant effect on production rates.
The same goes for product handling. A robotic depalletizer will process manufactured goods the same way, whether it may be five minutes or five hours. Even the most willing workers experience physical fatigue. If your product is depalletized in a more careless way as the day wears on, you risk losing time and money. Nothing is too heavy for a robot, and it will always get the job done at the same pace. A depalletizing machine will not only ensure stability, it will also give you a global perspective of your operations. What are your production rates? How many of one specific product can you process in an eight-hour shift? You will get answers to these questions through the Human Machine Interface (HMI). Getting feedback on your daily operations is essential to increasing profitability.
Uptime, speed, ROI: these are all benefits of automatic depalletizing. For maximum return, it is essential to invest in state-of-the-art equipment with an experienced supplier. The key question isn’t can you do it, but how will you get it done.