What Type of Pallet Wrapper Best Suits Your Needs?
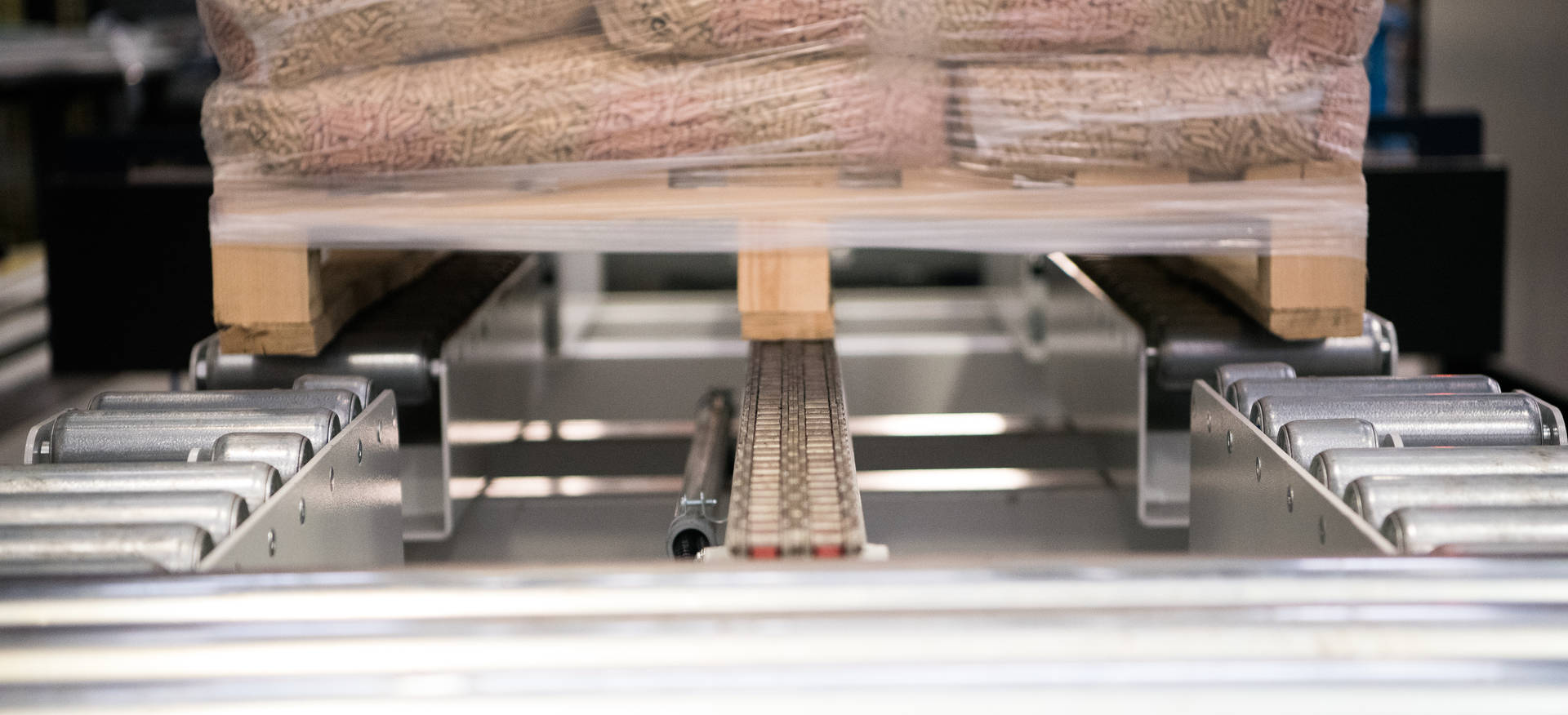
Pallet wrapping is a critical step in many industries to secure and protect goods during storage and transportation. While frequently the last step in your packaging line, it is certainly one of the most crucial aspects of the process.
Choosing the right pallet wrapping technology is essential to ensure the safety of your products, maximize efficiency, and improve your return on investment (ROI).
Three pallet wrapping technologies—turntable wrappers, rotary arm wrappers, and stretch hooders—each come with unique features and benefits. But the question remains, how do you select the best one for your specific needs?
In this article, we'll explore each technology and provide insights to help you make an informed decision:
Understanding your requirements
Before diving into the specifics of each pallet wrapping technology, it's crucial to assess your requirements. Consider the following factors:
- Load characteristics: What types of pallet loads do you work with? Are they primarily boxes, bags, or do you deal with irregularly shaped, fragile, or unstable loads?
- Wrapping volume: What is your current pallet wrapping volume, speed, and what goals are you aiming to achieve in terms of wrapping rate?
- Space constraints: What is the available floor space in your facility? Do you require a compact wrapper, or do you have enough space to accommodate a larger one?
- Budget: What is your allocated budget for pallet wrapping equipment?
- Load protection: After wrapping, where will the pallets be stored, and what are the environmental conditions in that storage area?
Now, let's delve into the characteristics and suitability of each pallet wrapping technology.
Different types of pallet wrappers
Hooders and wrappers share the common objective of securing loads; however, the decision between the two ultimately depends on your specific requirements. Exploring the distinct advantages offered by each method allows you to pinpoint the technology that aligns best with your needs.
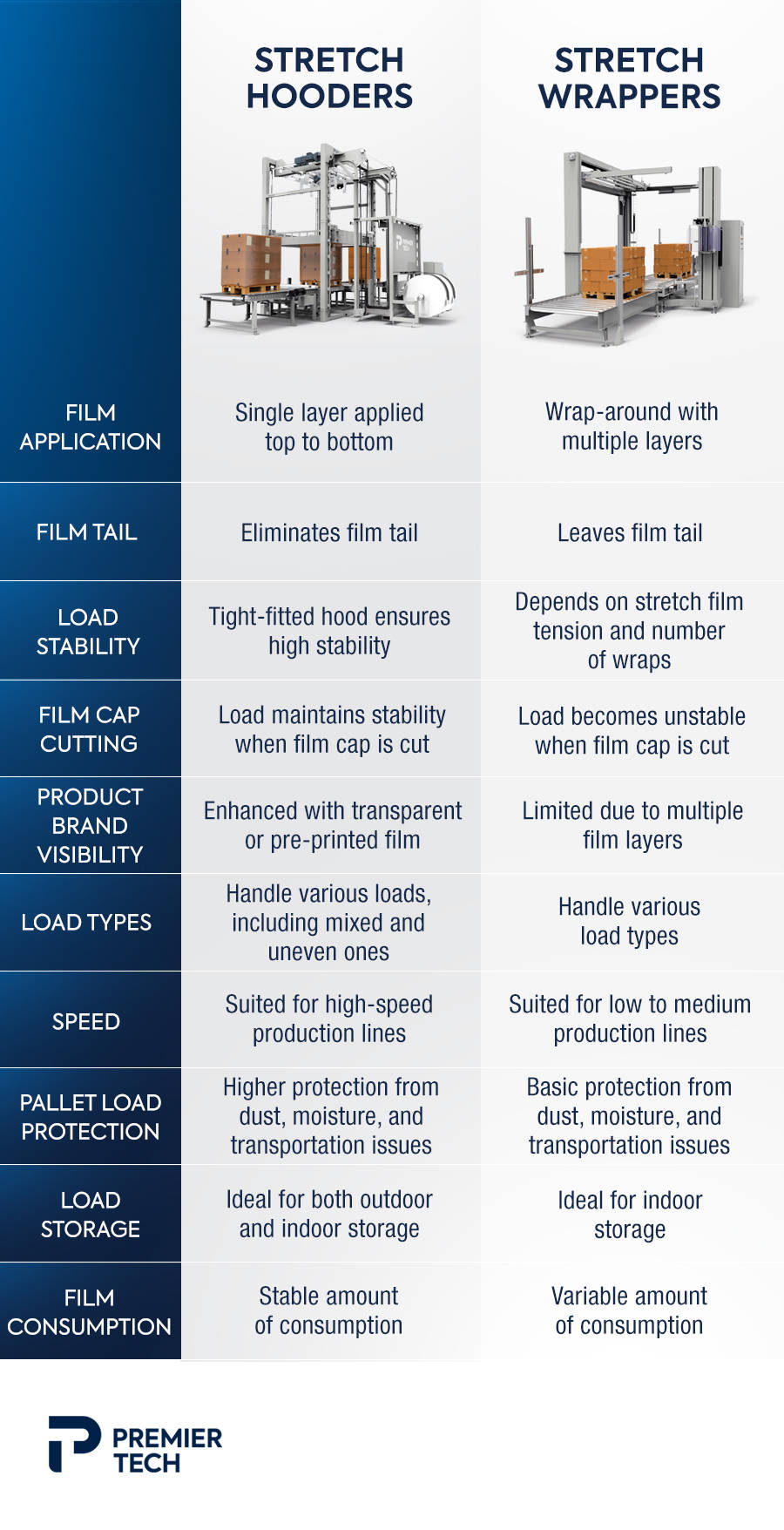
Stretch hooders
A stretch hooder is designed to apply a stretchable hood or sleeve made of stretch film to cover the entire palletized load. Stretch hood technology is incredibly versatile and can secure a wide range of pallet loads. This type of wrapping system offers unparalleled product safety and load stability. Stretch hooder machines do not require film cutting and wiping, unlike turntables and rotary arm technologies which often lead to film tails on your pallet loads.
The film is stretched and applied over the load creating a barrier against humidity, UV exposure, and other weather-related threats, as well as limiting the risk of cargo shifting during transport. Stretch hooding technology produces a tight-fitting hood. This hood can be transparent or pre-printed with your logo, making it the preferred choice for manufacturers who need brand visibility and load stability. Stretch hooders can wrap up to 100 loads per hour.
They are commonly used in industries where protection from weather conditions, dust, or contamination is essential, such as the construction industry, the chemical industry, the horticulture industry, or when packaging bulky or odd-shaped loads.
Consider stretch hooders if:
- Your pallet loads vary significantly in terms of size, shape, or stability.
- You require superior protection against external elements.
- Visibility of your product brand on the pallet is important.
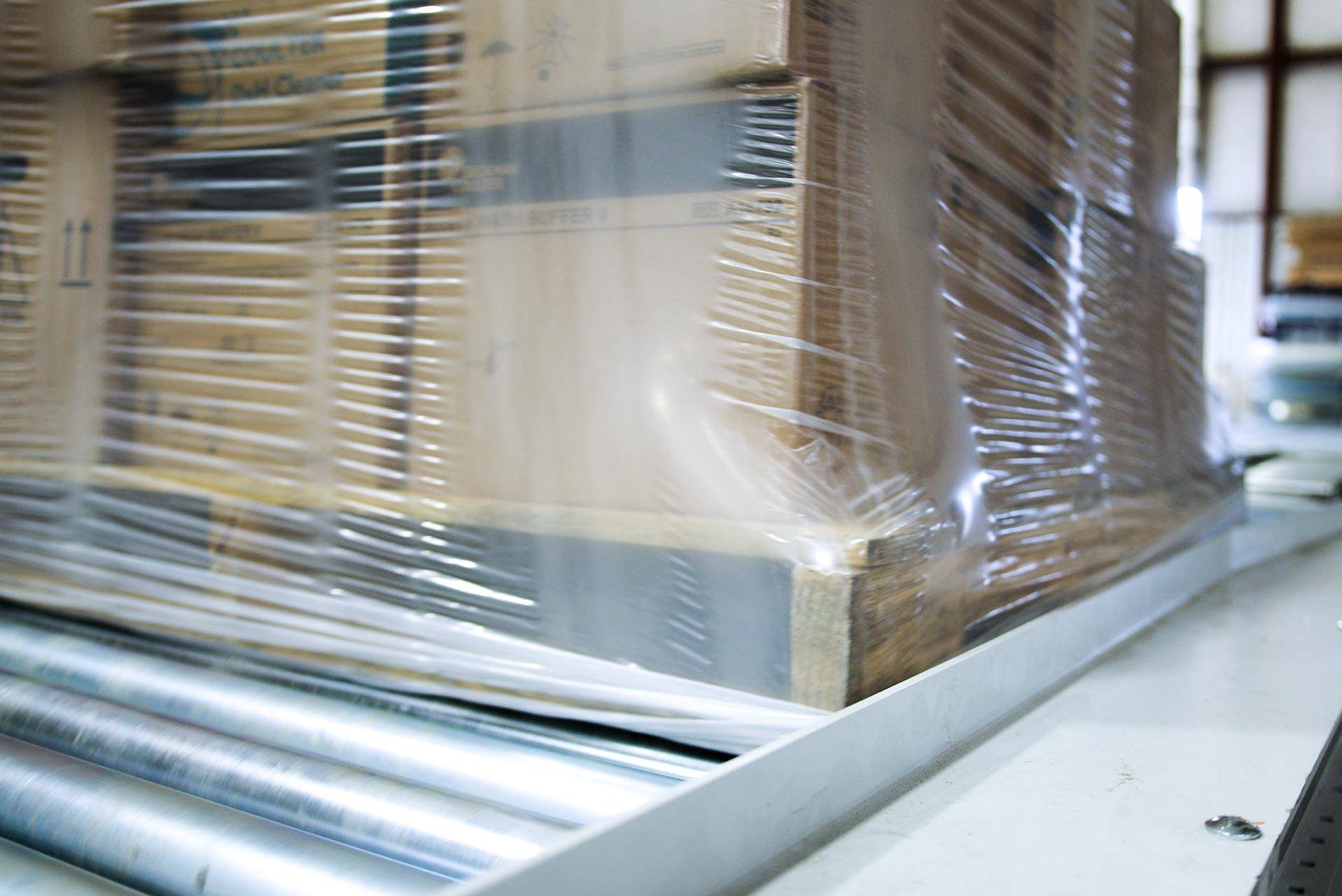
Stretch wrappers
Turntable wrappers
The turntable stretch wrapper places a load on a rotating turntable, which then dispenses the wrapping film. As the turntable spins, a film carriage moves up and down to wrap the stretch film around the load. They can wrap from 10 to 45 loads per hour, depending on the automation level and load height.
Turntable wrappers are known for their ability to consistently maintain the correct film tension, a key factor in successful stretch wrapping. A turntable wrapping machine is an excellent option for very stable loads and low-to-medium production rates.
Consider turntable wrappers if:
- You deal with stable, regularly shaped loads.
- Your production rate falls within the low range.
- Budget and space constraints are factors in your decision-making.
Rotary arm wrappers
The rotary arm stretch wrapper features a rotating arm equipped with a film carriage. Unlike turntable wrappers, the pallet remains stationary while the arm wraps the stretch film around the load by rotating above it. It allows for moderate to high-speed wrapping of loads, regardless of whether they are light, fragile, or heavy.
These machines are engineered to maintain consistent film tension and they are best suited for stabilizing palletized loads with regular or uniform shapes and dimensions. The rotary arm wrapper has a production rate ranging from 50 to 90 loads per hour in general and are commonly used in industries like warehousing, logistics, and distribution for securing pallets of goods.
Consider rotary arm wrappers if:
- Your load characteristics is of regular shapes and dimensions.
- You require moderate wrapping speed and load stability.
- You have the space and budget for a larger machine.
Automation levels
Apart from the three types of pallet wrappers mentioned, these machines are also available in varying degrees of automation: manual, semi-automatic, and automatic. Choosing the extent of automation that’s right for you depends on the packaging output you need to handle and your budget.
Manual wrappers
In manual wrappers, an operator applies the film manually. This level of automation suits low-output settings.
Semi-automatic machines
Semi-automatic machines, such as turntable wrappers and rotary arm machines, wrap loads automatically but require an operator to use a forklift to place the unwrapped load and pick up the wrapped one. They are suitable for moderate production levels.
Fully automatic equipment
Fully automatic wrappers employ conveyors to deliver loads, which are then automatically wrapped, cut, and sealed. They are ideal for high-output packaging operations.
In conclusion
Selecting the right pallet wrapping technology involves a careful assessment of your load characteristics, wrapping volume, space constraints, budget, and load protection requirements. Turntable wrappers, rotary arm wrappers, and stretch hooders each have their specifications.
Therefore, closely examine your situation to determine which pallet wrapper best suits your manufacturing process. Your investment in your product deserves the best protection.
By carefully considering these factors and choosing the right pallet wrapping technology, you can ensure your product reaches your customers in perfect condition, enhancing your ROI and maintaining the integrity of your brand.
Ready to get started with a pallet wrapper?
Now that you have a better understanding of turntable wrappers, rotary arm wrappers, and stretch hooders, along with the factors that influence your choice, take the next step. Evaluate your unique requirements, assess your budget, and explore the options available to you.