Carbon Black and Fumed Silica: The New Industrial Gold
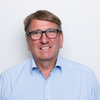
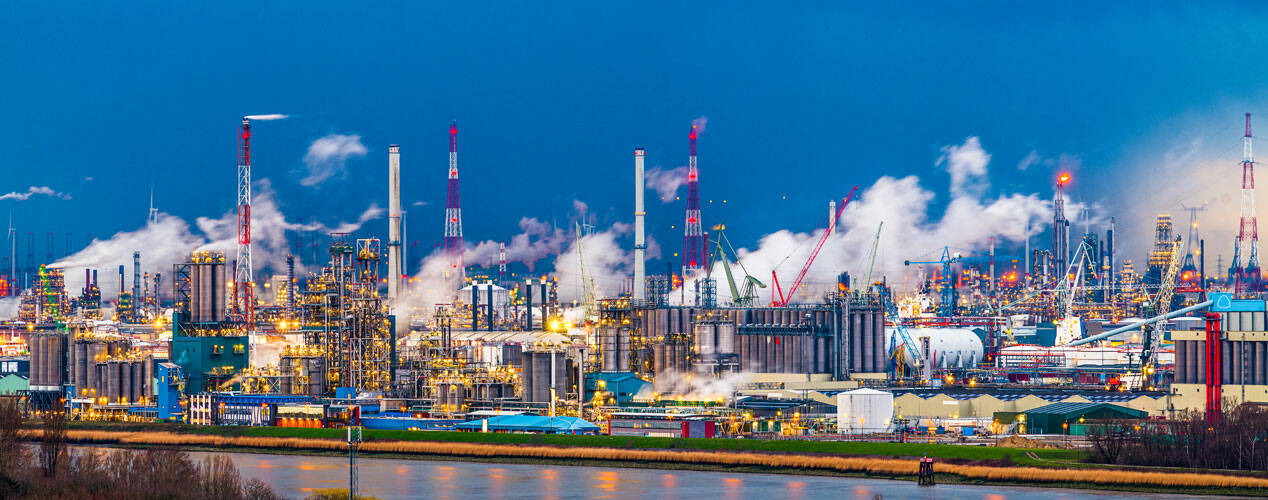
Reading time: 8-9 minutes
Carbon black and fumed silica are often referred to as the "new industrial gold" and are crucial to numerous industries. However, their production and refinement demand sophisticated techniques and stringent quality controls. Just as 19th century miners faced the arduous task of unearthing gold, scientists and engineers nowadays navigate the complexities of synthesizing and handling these valuable substances to unlock their full potential. Let us have a closer look.
" Carbon black and fumed silica are often referred to as the new industrial gold "
Carbon black: The unsung hero for modern industries
Carbon black is a fine, black powder made from the incomplete combustion of hydrocarbons. Traditionally it was used as a reinforcing agent in rubber products, such as tires, where it improves the strength and durability of the rubber. However, its uses extend to various industries:
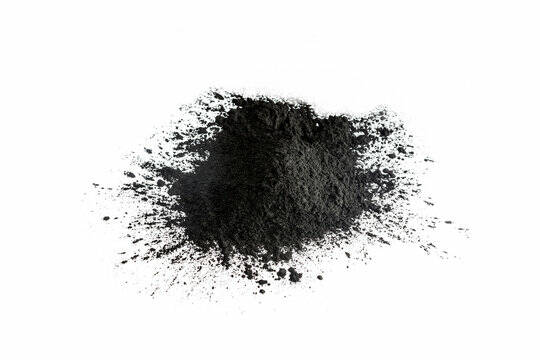
- Automotive industry: Carbon black is a key ingredient in the manufacture of tires, where it enhances the durability, wear resistance, and strength of the rubber. It also provides UV protection to prevent cracking and degradation.
- Pigments: It is used as a black pigment in inks, paints, coatings, plastics, and other coloring applications due to its deep black color and high opacity.
- Lubricants: It is used as a filler in certain lubricants and greases to improve their performance by enhancing wear resistance and reducing friction.
- Environmental applications: Carbon black is sometimes used in air and water filtration systems to absorb impurities.
- Electronics and conductive materials: Carbon black is used in the production of conductive materials, such as conductive coatings and capacitors. It can be found in anti-static materials and certain conductive polymers.
- Battery manufacturing: Carbon black is used in the production of batteries, particularly in the electrodes of lithium-ion and other types of batteries.
Fumed silica: The versatile marvel transforming industries
Fumed silica, also known as pyrogenic silica, is a fine, lightweight, amorphous form of silicon dioxide produced through a high-temperature flame hydrolysis process. Fumed silica's unique properties and wide range of applications make it an invaluable material in various industries, from cosmetics to electronics.
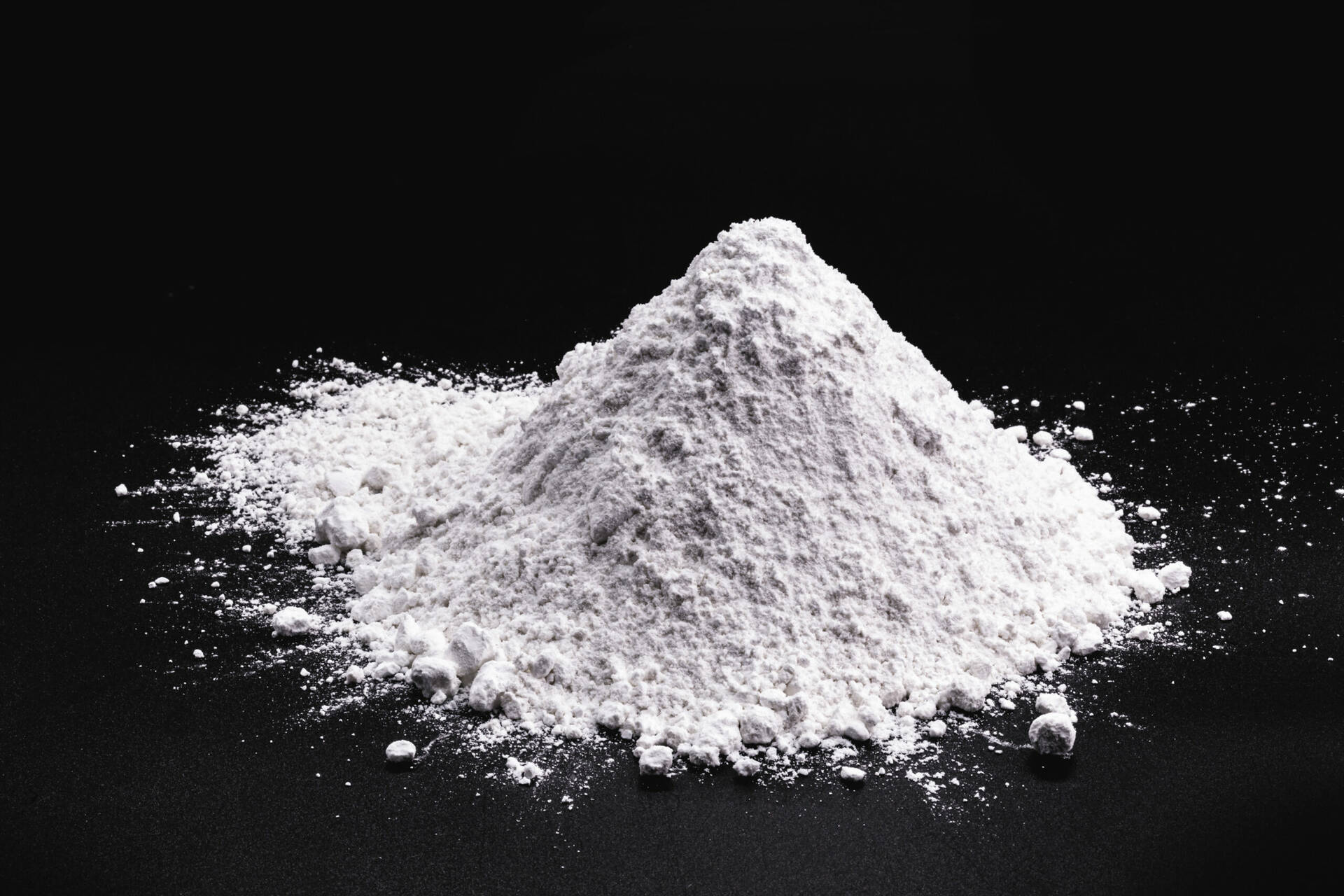
- Paints and coatings: Fumed silica is used as a thickening and anti-settling agent, providing stability and improving the application properties of paints and coatings.
- Adhesives and sealants: It enhances the viscosity and thixotropic properties of adhesives and sealants, ensuring they stay in place and perform effectively.
- Cosmetics and personal care: Fumed silica is used to improve the texture and spreadability of cosmetics, providing a smooth and silky feel. It also acts as a light-diffusing agent in makeup products. Whereas when incorporated into products like toothpaste, fumed silica provides mild abrasive properties for effective cleaning.
- Food and pharmaceuticals: As an anticaking agent, fumed silica ensures that powdered food products and pharmaceuticals remain free-flowing and easy to handle.
- Plastics and rubber: It is used as a reinforcing filler in silicone elastomers and other polymers, enhancing their mechanical properties and durability.
- Electronics: Fumed silica is used in the production of electronic components, such as encapsulants and coatings, to provide insulation and protection.
- Construction: It is used in construction materials like cement and concrete to improve their strength, durability, and workability.
Growing investments to meet growing demand
Overall, the increasing applications of carbon black and fumed silica in various industries will lead to a growing demand. The global carbon black market is projected to grow at a compound annual growth rate (CAGR) of around 6% from 2023 to 2033, whereas the global fumed silica market is expected to grow at a similar CAGR of 5%. This translates to an increase from $1.45 billion in 2024 to $2.36 billion by 2034 according to Fact.MR, a leading provider of syndicated and custom market research reports.
In recent years, investments in specialty chemical plants have grown significantly, with a strong emphasis on sustainability and circular economy principles, especially in carbon black. By focusing on recycling end-of-life products and utilizing alternative carbon sources, companies do not only aim to grow profitability, but equally aim to reduce environmental impact and meet the growing demand for eco-friendly materials across various sectors.
" In recent years, investments in specialty chemical plants have grown significantly, with a strong emphasis on sustainability and circular economy principles. "
A few examples highlighting the increased investment trend within the specialty chemical industry sector:
Circtec is constructing a flagship circular factory at the Chemical Cluster Delfzijl in the Netherlands. This facility will process used tires into green chemicals and materials, including biogasoline, carbon black, and reformed naphtha. The project represents an investment of €150 million and is expected to significantly contribute to CO₂ reduction and the circular economy. Construction commenced in May 2024, with support from investors such as Novo Holdings and A.P. Moller Holding.
Orion S.A., a global specialty chemicals producer, announced in September 2023 an investment of €12.8 million to develop and demonstrate a climate-neutral process for producing carbon black from alternative carbon sources. This initiative, known as the “Clean Carbon black Research and Development Project,” received half of its funding from Germany’s Federal Ministry of Economic Affairs and Climate Action, supported by the EU’s NextGenerationEU fund. The project involves constructing a research facility at Orion’s main innovation center in Cologne, Germany, and is designed to enhance yield and throughput in carbon black production using circular feedstocks, thereby significantly reducing the process’s carbon footprint.
In 2018, Birla Carbon Spain invested €5 million to increase their carbon black production capacity from 80.000 to 95.000 tons per year. This investment focused on sustainability and energy efficiency projects improving both productivity and environmental performance.
Evonik Industries invested €50 million in 2024 to expand its fumed silica production capacity at its Antwerp site. This project aims to meet the growing demand in the adhesives and sealants market while enhancing sustainability and energy efficiency.
High potential, difficult process
Processing specialty chemicals like carbon black or fumed silica can be challenging due to their fine, powdery nature and their tendency to agglomerate. They require precise control over particle size and quality, have specific safety and environmental requirements, and as such make the need for specialized equipment across the line extremely crucial. These factors complicate its integration into various products and processes, making it a material that requires careful management at every stage of production and application.
" Processing specialty chemicals can be challenging due to their fine, powdery nature and their tendency to agglomerate. "
Specialty chemicals as a whole can be bagged with vacuum packers, air valve packers or bottom-up fillers depending on the customer’s preference or the product characteristics. However, for carbon black and fumed silica, most often a vacuum packer is the preferred way due to their fine, powdery nature and their tendency to agglomerate.
Premier Tech Systems and Automation has over two decades of experience with vacuum packing and over 100 years with bagging in general. Premier Tech is among the leaders in vacuum valve bag fillers, and its legacy in vacuum bagging isn't just about the equipment; it also extends to its continued investments in research and development, and its close work within the industry itself.
These vacuum valve bag fillers are especially designed for packaging fine powders, such as carbon black and fumed silica. They are designed to handle fine lightweighted powders, making them ideal for materials that have small particle sizes and require careful handling to avoid dust and contamination. The integrated aspiration system and dust sensor effectively remove dust during the filling process, ensuring a clean and safe operation. The Premier Tech VPV vacuum valve bag filler is also capable of compacting bags up to 700%. This high compaction rate is particularly beneficial for these fine powders, as it helps to reduce the overall thickness of the filled bags. This allows for more efficient stacking on pallets, leading to significant cost savings in transport and storage.
In conclusion, carbon black, fumed silica, and vacuum valve bag fillers each play a crucial role in enhancing product performance and efficiency across various industries, with specialized equipment ensuring optimal handling and packaging.
Want to know more about packaging carbon black and fumed silica?
Contact us to discuss your specific needs with our experts.