3 Ways of Getting More Product to the Consumer for Wineries
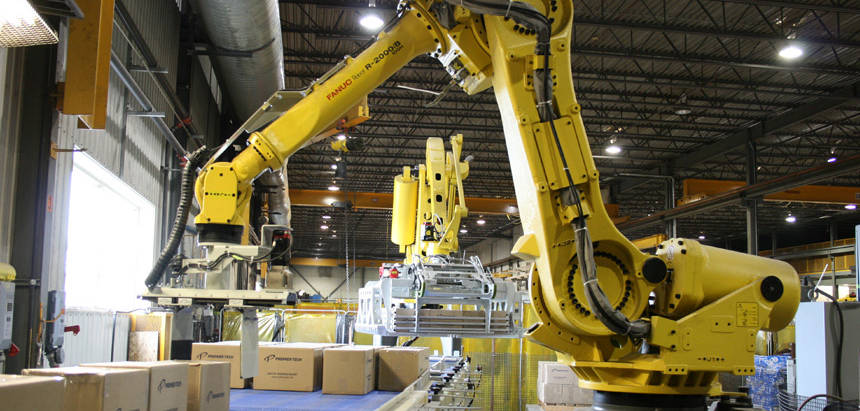
After 10 years of steadily increasing wine production, the United States now ranks as the 4th-largest wine producer in the world. More wineries are trying to find their place in an extremely competitive market. Unfortunately, in spite of the encouraging statistics, wineries both large and small are facing a number of major challenges. Delivering more product to consumers while preserving an acceptable profit margin is a core concern for wine producers in the United States.
The crucial phase where wine producers experience significant losses is the packing phase. In many ways, the packing of wine can quickly become a real headache. Inexperienced seasonal labour, frequent injuries, inappropriate load securing, product breakage and defects result in decreased profits which, over time, affect the profitability of wine producers. Here's 3 ways of getting more product to the consumer.
1. RISK-FREE BOTTLE HANDLING
Wineries spend a lot of money on aesthetics, so the packaging process needs to handle the product carefully, and fragility is a detrimental factor when it comes to wine case packing. The bottle needs to be handled gently to avoid scratches and breaks without compromising the speed. The winery needs to optimize their end of line with the case packer that will give them both speed and gentle handling.
Variable Frequency Drive
Automation of the case-packing process is an option that each winery should consider. While it may seem costly at first, installing an automated case packer should pay off for the business in the long term both by raising productivity and lowering spillage. Several types of case packers are equipped with dual-speed servo motors conveyors programmed to slow the movement when the bottle is handled directly, gently transport the product to the box, and then resume maximum speed. In this way, the packing line never stops and the risks are minimized. Variable frequency drives conveyors are the perfect solution to combine gentle handling and speed. This kind of feature is developed to fit the needs of many fragile products that need to be packed.
Custom-made gripper heads
To transport the bottles without damaging the glass or the label, manufacturers have to use custom-made gripper heads, also called “End effectors”, to secure and lift a cluster of bottles. Using the right packing equipment can improve the quality of the delivered product while reducing liability and cost of operation.
2. MINIMIZE RISK OF INJURIES
The fragility of the product is one of the factors to be considered when palletizing boxes of wine bottles. At this stage, the painstaking work is often done manually to avoid breakage and limit costs. However, short-term savings may quickly turn into long-term losses. Manual work is time consuming because the process slows down at the end of the line; on top of this, repetitive motions carry a risk of injury. In an industry where profit margins are so tight, this type of accident can be very expensive in terms of profitability.
Reduce Work force needs
Switching to automated palletizing also reduces packaging line workforce needs. Employees can be assigned to other duties and temporary workers are no longer needed. With this solution, you can significantly reduce the risk of injuries by replacing difficult manual labor. Considering that each 12-bottles case of wine your staff hoists weighs approximately 40 pounds, injuries are difficult to avoid with the do-it-yourself palletizing approach. The best decision for any winery is to basically engineer any potential hazard out of the plant.
Automated palletizers that fit your needs
For wineries, the key issue is affordability. A new generation of cost-efficient, small-footprint palletizers are available on the market, making it an easier investment decision even for slow-speed lines. The initial investment might appear high, the ROI has been proven through other installations.
3. ADEQUATE LOAD SECURING
Unfortunately, the load securing phase is the most overlooked, mainly due to lack of financial resources. Inappropriate load securing can produce a number of complications during transport, resulting in significant losses for producers. Today, many wineries still wrap their loads by hand, using less than ideal techniques performed by under-trained employees which increase the risk of losses.
Integrated pallet-wrapper
A well-secured load ensures secure transit and reduces damage claims. Who wants to pay to rewrap an inadequate load received at the warehouse? Using the right wrapping equipment for your needs can minimize warehouse and shipping damage, protect your loads against weather damage, dust or moisture and help prevent theft. While some producers may want to display their label by choosing a see-through wrapping film, others have very expensive products and want to hide their brand.
Producers need to choose the right material for their needs depending on pallet dimensions, shipping weight, uniformity of loads, shape, value, means of transportation and distance of transit. While the majority of U.S. wine is consumed locally, some well-known wineries still export their products all over the world and need specific technologies to wrap their loads efficiently.
There are three solutions wineries should consider when it comes to automating their load securing systems: Manual, Semi-Automatic and Fully Automatic equipment.
Manual Wrapping :
- Low cost
- Added to a manual packaging line
- Operator intervention
Semi-Automatic Wrapping:
- Easy to use
- Twice the wrapped load than with the manual
- Operator only has to push a button
Full Automation Wrapping :
- Unbeatable production rate
- No operator involved
- Custom solutions
WANT TO KNOW MORE ABOUT PACKAGING LINE AUTOMATION ?
Premier Tech Chronos is recognized worldwide for its innovative packaging and material handling solutions. Through numerous acquisitions made over the years, Premier Tech Chronos has integrated a great deal of technological knowledge and expertise. As a result, Premier Tech Chronos offers one of the most complete product portfolio in the industry, including case packers, palletizers, stretch wrappers, stretch hooders, unit and pallet conveyors. At Premier Tech Chronos, we are driven by innovation : In the past decade, the company has developed several state-of-the-art technologies that are still in the lead today. With many more to come, our prime objective is to continue to meet your needs in the most creative and efficient ways.