Un système d'ensachage et de palettisation est la clé du succès
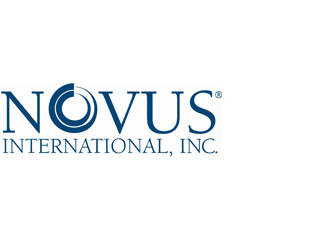
Un fabriquant de nourriture pour animaux procède à l’installation d’un système d’ensachage et de palettisation clé en main pour une nouvelle ligne de production.
Novus International Inc., dont le siège social se trouve à St. Charles au Missouri, est un fournisseur global d’ingrédients pour nourriture pour animaux et d’autres produits pour la volaille, le bétail, les cochons, les chevaux, les animaux domestiques, et plus encore. Son usine de Little Rock en Arkansas produit et exporte des ingrédients vers plus de 70 pays. En 2009, la compagnie a agrandi l’usine de Little Rock afin d’augmenter sa production et ainsi être en mesure de satisfaire la demande croissante. Pour s’assurer que les divers produits soient adéquatement ensachés, palettisés et préparés pour le transport, Novus International Inc. avait besoin d’un système d’ensachage et de palettisation automatisé à la fois rapide, fiable et précis.
Trouver un système clé en main
Pendant qu’elle était à la recherche du système d’ensachage et de palettisation, l’entreprise a fait part de ses exigences aux meilleurs fournisseurs de systèmes d’emballage en Amérique du Nord, et leur a demandé des soumissions. La compagnie devait remplir avec précision des sacs à gueule ouverte de type « pinch-bottom » de 25 kg, à raison de 14 sacs par minute, ainsi que des sacs de polypropylène tissé à valve ouverte de 1 000 kg, à raison de 12 sacs par heure. En ce qui concerne les sacs de 25 kg, il fallait pouvoir manutentionner trois types différents : des sacs en papier à parois multiples, des sacs en papier à doublure plastique et des sacs en polyéthylène à faible densité. De plus, la compagnie devait s’assurer que les sacs palettisés seraient bien protégés durant le transport.
« Nous voulions un système automatisé complet et clé en main, et souhaitions que toutes les composantes proviennent du même fournisseur », explique Kevin Mowery, directeur principal des opérations et de la chaîne logistique chez Novus. «Pendant le processus d’évaluation des soumissions, nous avons trouvé un fournisseur qui avait bien compris nos besoins et était très professionnel dans son approche globale. Nous avons vérifié ce que pensaient les clients chez qui ils avaient installé des équipements semblables, et ceux-ci étaient tous très satisfaits, non seulement en ce qui a trait aux équipements, mais aussi par rapport au soutien technique reçu. De plus, certains de nos équipiers avaient déjà eu des expériences positives avec ce fournisseur alors qu’ils travaillaient sur d’autres projets pour d’autres compagnies.»
Puisque ses produits se composent de particules granulaires à écoulement libre de différentes tailles, la compagnie a envoyé plusieurs échantillons ainsi que les trois types de sacs au fournisseur pour qu’il fasse des tests. Des équipiers de chez Novus se sont rendus chez le fournisseur afin d’assister à ces tests, lesquels ont démontré que les taux d’ensachage et les niveaux de précision requis pouvaient être atteints.
« Toutefois, nous voulions nous assurer qu’ils pouvaient livrer le niveau de performance que nous recherchions, à grande échelle. Nous avons donc aussi visité une usine près de leur siège social, et une autre près de chez nous, afin de voir le système en action », raconte Mowery. «L’une des choses que nous avons remarquées, c’est la robustesse de leur équipement : on peut tout de suite voir que les structures sont très résistantes et de qualité supérieure. Nous avons aussi aimé le fait de pouvoir se procurer auprès d’un détaillant local des pièces de rechange pour les composantes comme les servomoteurs. Cela minimise les temps d’arrêt et les coûts d’entretien, puisque ces pièces sont disponibles plus rapidement et à moindre prix. Nous sentions que le système intégré du fournisseur ferait le travail et durerait longtemps. Nous avons donc décidé d’en acheter un pour notre usine.»
Le système d’ensachage et de palettisation
Le nouveau système automatisé clé en main se compose d’un système de pesage, d’une ensacheuse pour sacs à gueule ouverte, d’un convoyeur à courroie, d’un palettiseur à empilement par le haut, d’une ensacheuse pour grands récipients pour vrac souples (GRVS), d’un convoyeur à rouleaux, d’une housseuse à film étirable, d’un automate program-mable, de divers équipements auxiliaires et de capteurs. L’équipement est arrivé à l’usine de Little Rock à l’automne 2010, et le fournisseur a envoyé plusieurs techniciens pour aider la compagnie avec l’installation et la mise en service. En novembre 2010, la compagnie a démarré le nouveau système automatisé sans problème et a commencé à ensacher et palettiser des produits la même journée.
Le système d’ensachage et d’emballage intégré est programmé pour permettre à la compagnie de remplir des sacs de 25 kg et 1 000 kg de façon simultanée, ce qui garantit que les taux de production requis sont toujours atteints. Pour remplir les sacs de 25 kg, la compagnie amène un produit dans une trémie installée au-dessus d’un doseur gravitaire à haute vitesse E-55GHS qui alimente une doseuse à poids net électronique E55-NXT. Le doseur servocommandé est contrôlé par la peseuse et commence à alimenter par gravité à pleine capacité. Lorsque le poids fixé est presque atteint, sa porte commence à se refermer tranquillement en fonction du poids qui augmente. Celle-ci se ferme complètement au moment précis où le poids cible est obtenu. Selon Anthony Siblall, directeur des ventes chez Premier Tech, ce mode d’alimentation permet d’obtenir des vitesses d’alimentation plus éleves ainsi que des poids plus précis qu’avec les doseurs typiques à alimentation lente.
Tandis que la peseuse alimente l’ensacheuse automatique haute vitesse PTK-1700, l’unité de ramassage de l’ensacheuse prend un sac vide dans le magasin, le déplie, l’ouvre et le place sur le bec de remplissage anti-poussière. Le sac est ensuite rempli par gravité. Un dépoussiéreur intégral retire l’air déplacé et la poussière du sac pour une opération d’ensachage des plus propres. Un système de tassement aide à désaérer le produit pendant que le sac se rempli. Le sac rempli est transféré vers un convoyeur de sortie qui déplace le sac dans le système de scellage jusqu’à l’imprimante à jet d’encre, pour des étiquettes sur mesure.
À partir de l’imprimante, le sac se déplace vers un culbuteur de sacs qui le couche à plat sur un convoyeur à courroie. Celui-ci déplace le sac vers un détecteur de fuite qui avertit le système de rejet des sacs si le sac doit être retiré de la ligne. Le sac est ensuite transporté vers l’aplatisseur de sacs qui l’aplatit et le prépare pour la palettisation. Ensuite, le sac passe par le contrôleur de poids et le détecteur de métal avant d’atteindre un convoyeur à gravité court équipé d’un système de rejet des sacs. Si un sac se trouve en dehors de l’échelle de précision fixée, le contrôleur de poids informe le système de rejet des sacs qu’il faut le retirer de la ligne. S’il y a du métal dans le sac, celui-ci est marqué par le détecteur de métal et le système de rejet des sacs le retire de la ligne, ce qui permet aux opérateurs de facilement différencier les sacs.
Après être passé par le convoyeur par gravité, le sac est déplacé vers le palettiseur de sacs automatique à empilement par le haut AP-425, qui est équipé de distributeurs automatiques de palettes vides et de feuilles de palettisation. Il peut palettiser jusqu’à 25 sacs par minute selon un modèle à 5 sacs. Le système de rotation standard fait tourner le sac et l’oriente en fonction du modèle préprogrammé, puis le place sur la palette. Lorsqu’une couche de sacs est complétée, l’élévateur de palettes électrique à deux vitesses du palettiseur s’abaisse pour qu’une autre couche de sacs puisse être complétée. Le palettiseur alterne le modèle d’empilage de chaque couche afin de garantir la stabilité de la palette.
Pendant que l’ensacheuse pour sacs à gueule ouverte est en opération, la compagnie peut envoyer un produit dans une trémie installée au-dessus de l’ensacheuse automatique pour GRVS BG-931. Cette ensacheuse place automatiquement une palette vide sur la plateforme de la peseuse de l’ensacheuse, située juste en-dessous de la sortie de la trémie. La plateforme est montée sur quatre cellules de charge qui communiquent le poids du sac à l’automate programmable de l’ensacheuse lors du remplissage. Une fois la palette en position, l’opérateur suspend manuellement un sac vide au porte-sacs de l’ensacheuse et insère un bec de remplissage à double paroi avec une bande extensible dans la valve ouverte du sac afin de créer un sceau anti-poussière. Lorsque le produit s’écoule par le tube central du bec, l’air déplacé et la poussière sont évacués par le dépoussiéreur, par le tube extérieur du bec.
Une fois que l’opérateur a activé l’ensacheuse, le doseur gravitaire haute vitesse E-55GHS alimente le sac à partir du trémie. Un vibrateur fonctionne par intermittence pour aider à tasser le produit dans le sac. Lorsque le poids cible est atteint, l’opérateur relâche les poignées du sac et retire le bec de remplissage. Les rouleaux motorisés de la plateforme envoient ensuite la palette complétée sur le convoyeur à rouleaux motorisé, qui la déplace jusqu’au contrôleur de poids, et ensuite vers la housseuse. Si un sac se trouve en dehors de l’échelle de précision fixée, le système s’arrête et une alarme est déclenchée pour qu’un chariot élévateur puisse retirer la palette de la ligne. Afin de garantir un produit exempt de tout contaminant, un détecteur de métal installé dans la ligne de convoyage, juste avant la trémie, fait dévier tout produit contaminé en dehors de la ligne et ferme le système pour alerter l’opérateur.
Le convoyeur à rouleaux motorisé déplace les palettes complétées provenant du palettiseur et de l’ensacheuse vers la même housseuse. Des capteurs installés sur le convoyeur contrôlent le débit, en priorisant les palettes provenant du palettiseur et permettant à la compagnie d’opérer les deux lignes en même temps. La housseuse place une housse de film par-dessus les sacs pour fixer la charge à la palette et la protéger contre l’humidité. La housse de film exerce une tension à la fois verticale et horizontale sur la charge en la poussant légèrement sur la palette, ce qui améliore la qualité d’emballage des charges lourdes ou instables.
Une fois la charge fixée, les palettes passent par une étiqueteuse à quatre côtés, qui applique une étiquette sur les côtés de la housse de film. Elles se retrouvent ensuite sur un convoyeur à butée, où elles attendent qu’un chariot élévateur les amène à l’entrepôt.
Le système d’ensachage et de palettisation utilise cinq automates programmables : un pour l’ensacheuse, un pour le palettiseur, un pour la housseuse, un pour l’ensacheuse pour GRVS, et un pour les capteurs de contrôle du débit. L’automate programmable de l’ensacheuse est intégré à celui du palettiseur, ce qui permet aux opérateurs d’apporter des modifications aux paramètres des deux équipements à partir du même endroit. Pour garantir une utilisation sécuritaire de l’équipement, des rideaux lumineux sont installés à des endroits stratégiques. Si un rideau lumineux est brisé ou interrompu (par le bras d’un opérateur ou un débris volant, par exemple), le système se ferme automatiquement.
Ensachage rapide et précis
Depuis l’installation du système d’ensachage et de palettisation, la compagnie remplit des sacs aux taux requis, avec des niveaux de précision de ±56 grammes à 2 Sigma pour les sacs de 25 kg et de ±454 grammes à 2 Sigma pour les sacs de 1 000 kg. « La capacité de l’ensacheuse à manutentionner différents types de sacs permet de fournir aux clients exactement ce qu’ils veulent», explique Mowery. «Le palettiseur fait un bon travail. Les sacs sont bien placés, les palettes ont belle allure. Nous aimons aussi le design de la housseuse et le fait qu’elle fonctionne très bien. Puisque la housse de film se glisse par-dessus les sacs et la palette afin de fixer la charge, cela donne une palette plus stable et mieux protégée contre les intempéries lors du transport. Cela est important pour nous parce que nous exportons beaucoup de nos produits outre-mer dans des conteneurs, et nous voulons que les palettes et les produits soient intacts et en parfaite condition lorsqu’ils arrivent chez le client.»
Selon Mowery, le fournisseur a livré un système d’ensachage et de palettisation clé en main à la fois rentable, efficace et fiable. «Le système est complètement intégré, et ils ont assumé la responsabilité pour tous les équipements, même s’ils ne l’avaient pas fabriqué. Nous obtenons donc tout le soutien qu’il nous faut en appelant au même numéro. Le système est facile à nettoyer et nous fournit un ensachage sans poussière ni dégât qui combine rapidité et précision. Il a été facile pour nos opérateurs d’apprendre à l’utiliser, et il ne faut qu’un opérateur par quart de travail pour le faire fonctionner.
Le fournisseur a été réceptif et a fait preuve de beaucoup d’expertise. Il nous offre un excellent soutien lorsque nous en avons besoin, ce qui permet de minimiser les temps d’arrêt et d’optimiser les taux de production.»