Automatiser ses opérations d'ensachage grâce à la mise à jour d'une ensacheuse par aspiration
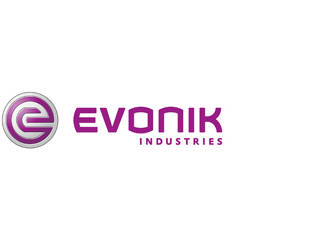
La compagnie Evonik-Degussa, dont le siège social est situé à Parsippany, au New Jersey, possède une usine à Waterford, dans l’État de New York. Cette dernière produit et emballe du dioxyde de silicium (SiO2) hydrophile (qui absorbe l’eau) et hydrophobe (qui repousse l’eau). Le dioxyde de silicium est utilisé comme charge dans des produits tels que de la peinture, des adhésifs, des enduits et des produits de calfeutrage à base de silicone.
À l’usine de Waterford, il est produit en grande quantité et expédié aux utilisateurs dans divers types de contenants, des sacs de 10 lb aux wagons porte-rails. Quand l’usine a commencé sa production en 1992, elle utilisait des ensacheuses manuelles par aspiration afin de remplir des sacs à valve en papier dans des formats de 10 et 20 lb et de 10 et 15 kg. Cependant, la manutention manuelle des sacs entraînait plusieurs problèmes d’ergonomie. La compagnie a donc décidé d’automatiser ses opérations d’ensachage et de palettisation en vue d’améliorer l’ergonomie de la ligne d’ensachage.
Ensacher et palettiser du SiO2
L’usine de Waterford fait partie du secteur « matériaux inorganiques » de la compagnie. Elle fonctionne 24 heures par jour, 7 jours par semaine; la ligne d’ensachage fonctionne donc tous les jours pendant deux quarts de travail de 12 heures. Initialement, la ligne d’ensachage utilisait deux ensacheuses manuelles par aspiration afin de remplir de dioxyde de silicium différents formats de sacs à valve en papier. Quelques années plus tard, la production a augmenté, et la compagnie a ajouté une troisième ensacheuse manuelle par aspiration. Aux stations d’ensachage et de palettisation, les opérateurs devaient manipuler les sacs manuellement.
Selon Mark Honeyman, superviseur de l’ingénierie de maintenance pour l’unité d’affaires Aerosil Silanes (Amérique du Nord), la manutention manuelle des sacs aux stations d’ensachage et de palettisation causait plusieurs problèmes. « L’un de nos problèmes majeurs concernait l’ergonomie de la ligne d’ensachage et les pertes de temps liées aux accidents, affirme Honeyman. Lorsqu’un opérateur effectuait un faux mouvement ou se blessait en travaillant avec une ensacheuse par aspiration ou à la station de palettisation, il devait prendre congé pour se rétablir. Un autre problème concernait la précision de remplissage de nos ensacheuses. Étant donné que leur système de pesée n’était pas très précis, elles avaient souvent tendance à remplir les sacs trop ou pas assez. Et comme la ligne d’ensachage était manuelle, elle n’arrivait pas à suivre le rythme de la ligne de production et créait un goulot d’étranglement. » Afin d’améliorer la performance de sa ligne d’ensachage, Honeyman a contacté le fournisseur Groupe Équipements Industriels de Premier Tech (IEG) et a demandé s’il était possible d’effectuer une mise à jour de l’une des ensacheuses par aspiration en y ajoutant un placeur de sacs et un scelleur automatiques. IEG, dont le siège social est situé à Rivière-du-Loup, au Canada, fournit des systèmes d’ensachage, de procédés, de pesée, de tamisage et de triage. Ceux-ci sont destinés entre autres aux industries des produits chimiques et pharmaceutiques, des minéraux, de la nourriture humaine et animale et des matériaux de construction. L’entreprise avait récemment développé le placeur de sacs à valve et scelleur à ultrasons DB-810, qui pouvait s’intégrer à l’ensacheuse manuelle par aspiration de Degussa. Les équipements ont donc été expédiés à l’usine de Waterford; en octobre 2004, Honeyman les a installés en collaboration avec des ingénieurs d'IEG. « Après l’automatisation de la première ensacheuse, nous avons constaté une amélioration de l’efficacité de la ligne d’ensachage et une augmentation de la production, se rappelle Honeyman. Les opérateurs ont beaucoup apprécié l’ensacheuse manuelle, car ils n’avaient plus à manipuler manuellement autant de sacs que par le passé. De plus, lorsque le fournisseur a mis à jour l’ensacheuse, il a également remplacé le système de pesée par un système beaucoup plus performant qui a grandement amélioré l’efficacité et la constance du remplissage des sacs. »
Après avoir bénéficié pendant plus de deux ans des avantages de l’ensacheuse automatisée, Honeyman a décidé d’automatiser la deuxième ensacheuse manuelle par aspiration à l’aide d’un système d'IEG. Et cette fois-ci, il voulait également automatiser les opérations de palettisation de la ligne d’ensachage afin de réduire davantage les problèmes d’ergonomie causés par la manutention manuelle des sacs. Honeyman a donc communiqué avec IEG et, en discutant de son projet, a appris que la deuxième ensacheuse pourrait être équipée d’une version améliorée du DB-810. Evonik-Degussa a donné son approbation à ce nouveau système; en décembre 2006, un placeur de sacs à valve et scelleur à ultrasons DB-815 a été ajouté à la deuxième ensacheuse. Quant aux opérations de palettisation, elles ont été automatisées grâce à l’installation d’une cellule de palettisation robotisée AR-200. (Une cellule de palettisation robotisée comprend un robot et tous ses équipements auxiliaires tels que des convoyeurs, des distributeurs de palettes et des distributeurs de feuilles de fond; le tout est entouré d’une clôture de sécurité.) Tout comme la fois précédente, le fournisseur a mis à jour le système de pesée afin d’en améliorer la précision lors du remplissage.
Les ensacheuses par aspiration automatisées et la cellule de palettisation robotisée
Les systèmes DB-810 et DB-815 ont un fonctionnement similaire, mais le premier utilise la pneumatique tandis que le second utilise l’électromécanique. Depuis que ces systèmes ont été intégrés aux ensacheuses, l’opérateur qui travaille à la station d’ensachage doit uniquement placer des sacs vides dans le magasin de sacs : le reste du processus est automatisé. « Par le passé, l’opérateur devait retirer le sac de la bouche d’ensachage et refermer la valve manuellement », explique Gary Ritter, coordonnateur ventes chez IEG. « En plus d’entraîner des problèmes d’ergonomie, ce procédé faisait en sorte que de la poussière s’échappait du sac. Les sacs de papier utilisés maintenant ont une valve externe dont l’intérieur est recouvert d’une couche de plastique. La chaleur et la pression générées par le scelleur à ultrasons font fondre le plastique, auquel une pression est appliquée afin de créer un sceau étanche. » La cellule de palettisation robotisée AR-200 avec un seul bras robotique comprend deux stations de palettisation, lesquelles reçoivent des sacs remplis en provenance de lignes de convoyeurs différentes. Une ligne de convoyeurs relie le DB-815 à la première station de palettisation, et une autre relie l’ensacheuse manuelle à la deuxième station de palettisation. Le DB-810 peut être relié à l’une ou l’autres des stations de palettisation, selon le produit ou le format de sac traité. Étant donné que la compagnie ensache deux produits différents et utilise quatre formats de sacs, le palettiseur peut être programmé afin d’empiler simultanément deux formats de sacs sur deux palettes différentes, avec un patron de palettisation différent pour chaque palette. L’opérateur doit simplement sélectionner le format de sac et la station de palettisation; les renseignements préprogrammés dans la mémoire du palettiseur lui permettent de déterminer où empiler les sacs et selon quel patron.
Afin que les sacs aient tous un poids identique, chaque ligne de convoyeurs comprend un convoyeur peseur qui est relié au palettiseur. Lors de leur passage sur le convoyeur peseur, tous les sacs sont pesés. Si leur poids est anormal, le bras robotisé les transfère vers un convoyeur de rejet. Le système est programmé de façon à ce que l’ensacheuse appropriée s’arrête dès que le palettiseur ne reçoit plus de sacs en provenance d’une ligne de convoyeurs. De plus, une série de capteurs disposés tout au long de la lige crée un système à sécurité intégrée : s’il y a un problème sur la ligne d’ensachage, peu importe l’endroit, les ensacheuses vont s’arrêter. Par exemple, s’il n’y a plus de palettes vides pour alimenter le palettiseur, un capteur va demander à la ligne d’ensachage de s’arrêter étant donné qu’il n’y a plus de palettes pour empiler les sacs. Maintenant, Degussa a besoin de seulement deux opérateurs pour faire fonctionner l’ensemble de la ligne d’ensachage. Le premier travaille sur une mezzanine, d’où il observe les ensacheuses automatisées et vérifie si les magasins de sacs sont remplis. Le deuxième travaille sur le plancher de l’usine, à la cellule de palettisation robotisée; il s’assure que les distributeurs de palettes vides et de feuilles de fond sont remplis et retire les palettes pleines de la station d’accumulation.
Améliorer les opérations d’ensachage et de palettisation
Depuis l’automatisation des deux ensacheuses par aspiration et l’installation de la cellule de palettisation robotisée, la compagnie a constaté une augmentation considérable de sa productivité. « Nous avons amélioré l’ergonomie de la ligne s’ensachage tout en augmentant sa production », affirme le Dr Hauke Jacobsen, directeur d’usine. « Maintenant, il nous suffit de faire fonctionner les deux ensacheuses automatisées, car elles arrivent à suivre la cadence de la ligne de production. De plus, comme les ensacheuses automatisées assurent un remplissage plus précis et plus constant, nous n’avons plus un nombre élevé de sacs trop pleins ou pas assez remplis. Par ailleurs, le scelleur à ultrasons produit un sceau étanche à la poussière qui prévient les fuites, et le palettiseur empile les sacs selon un patron serré, ce qui augmente la stabilité des palettes. Je suis très satisfait de la solution que nous avons trouvée. »
L’automatisation des ensacheuses et des opérations de palettisation a réduit les besoins en main-d’œuvre de la compagnie. Honeyman affirme : « Maintenant, les opérateurs qui travaillent sur la ligne d’ensachage disposent de plus de temps libre pour effectuer d’autres tâches comme l’entretien et les inspections, car ils ne sont plus enchaînés à une machine spécifique ou à une tâche manuelle répétitive. »