Vulmachine biedt oplossing aan maalderij
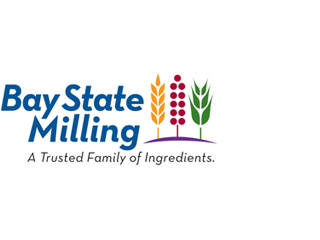
Flour power
Een maalderij verhoogt haar productiesnelheid met 85% en verlaagt het aantal arbeidsuren door flexibele schroeftransporteurs, netto-weegschalen en open-mondvulmachines met dubbele vulbuizen te installeren.
Bay State Milling Company, een in Massachusetts gevestigd bedrijf, had een benijdenswaardig probleem: haar vestiging in Clifton, New Jersey, kon niet aan de vraag naar meel van de klanten voldoen. "We moesten voldoen aan de vraag van nieuwe klanten", vertelt Plant Manager Mike Walsh. "We hadden een snelle verpakkingsmachine met snelle omschakelingsmogelijkheden nodig, eentje die ook veelzijdig genoeg was om zakken van 100, 50 en 25 pond op dezelfde machine te verwerken." En dat was nog niet alles, want het witte en volkorenmeel en het roggemeel waar de nieuwe klanten van Bay State Milling om vroegen, moest zeer nauwgezet vrij worden gehouden van vervuiling in de lucht en van vocht. Dat was van essentieel belang om te kunnen voldoen aan de strenge hygiënevoorschriften voor food-grade toepassingen, en om het risico op een stofexplosie te vermijden. Dat risico neemt toe naarmate het bloem vocht absorbeert. En alsof deze eisen nog niet genoeg waren, was het vloeroppervlak in de fabriek ook nog beperkt.
De oplossing op zak
Een vulmachineoplossing met kleine afmetingen die aan alle eisen van Bay State Milling voldeed, kon gelukkig worden geleverd door het in Quebec gevestigde Premier Tech. De vulmachine van het model PTK-2700 die door de leverancier werd geïnstalleerd, is een high-speed netto-gewicht openmondverpakkingssysteem met dubbele vulbuizen, waardoor Bay State Milling twee keer zoveel zakken per tijdseenheid kan vullen. Het meel wordt naar de vulmachine getransporteerd door twee flexibele schroeftransporteurs van het model DSR, die het materiaal naar een door Premier Tech ontworpen massastroomhopper brengen. De hopper is geïnstalleerd boven twee model E55 netto-weegschalen die boven de vulmachine hangen, waarbij elke schaal aan de eigen vulbuis aan de vulmachine is gekoppeld.
Verstandige keuzes
Flexibel schroeftransport was om verschillende redenen de juiste methode om meel te verwerken. Ten eerste transporteert een flexibele schroeftransporteur het materiaal mechanisch in een omsloten buis. Dit betekent dat meelstof in de buis blijft, waardoor de kans op een stofexplosie kleiner wordt, de locatie schoner wordt gehouden en medewerkers beschermd zijn tegen zowel explosies als het inademen van stof. Ten tweede worden vocht en vervuiling in de lucht uit het meel gehouden, omdat er in dit proces geen lucht wordt gebruikt als transportmedium. Dat is niet alleen nodig voor de hygiëne, maar ook omdat meel moeilijk te verwerken wordt als het zich vermengt met lucht.
"Meel is fluïdiseerbaar, en dus is ons doel om lucht zo veel mogelijk uit het meel te houden, want anders wordt het vullen van een zak een nachtmerrie," waarschuwt Jonathan Levesque van Premier Tech die optrad als projectmanager. Ten derde was de beperkte ruimte in de fabriek ook een goed argument voor het gebruik van een flexibele schroeftransporteur, omdat deze relatief kleine afmetingen heeft en omdat hij in een grote verscheidenheid van configuraties kan worden geïnstalleerd. Tenslotte was het feit dat dit type transporteur een constante stroom van materiaal levert een doorslaggevende factor in zijn voordeel.
Nauwkeurige afvulling
Dat komt omdat de stroom van het materiaal in de weegschalen "zo constant mogelijk moet zijn om een goede weegnauwkeurigheid te krijgen," benadrukt de heer Levesque. "De schroef biedt deze constante stroom." Het vulsysteem kan dit realiseren omdat "het twee schroeven bevat, een grote en een kleine," vervolgt hij. "De aanvoer geschiedt in twee stappen, die we bulkfase en druppelfase noemen. Eerst [bij het vullen van de hopper] laten we beide schroeven op volle snelheid draaien voor de bulkfase. Daarna, als de schaal in de buurt van het ingestelde doelgewicht komt, schakelen we de grote schroef uit en laten we alleen de kleine schroef langzaam doordraaien in de druppelfase" totdat het doelgewicht is bereikt. De doelgewichtnauwkeurigheid — de gewichten variëren minder dan 85 g op 2 sigma — was een belangrijke factor voor Bay State Milling’s keuze voor de E55. Feedback over de prestaties, statistische gegevens en meerdere weegprogramma's die deel uitmaken van de weegcontroller van de schaal stellen Bay State Milling in staat om de productie te fine-tunen en een langetermijnplanning op te stellen.
Vullen
Nadat via de vulhopper meel naar de schalen die boven de vulmachine hangen is gebracht, sturen de weegschalen op hun beurt meel door naar de vulbuizen van de vulmachine met behulp van een door Premier Tech ontworpen afleverhopper. De afleverhopper levert meel aan twee zakken en houdt tegelijkertijd stof tegen. Stof wordt ook gereguleerd door het zakdetectiesysteem bij de vulbuizen, omdat automatische zakweigering voorkomt dat meel wordt afgeleverd tenzij er een zak aan de vulbuis is geplaatst. Geweigerde zakken worden automatisch verwijderd en nieuwe zakken op de vulbuizen geplaatst. Wanneer het tijd is om een ander formaat zak te vullen, geschiedt de omschakeling met behulp van een touch-screen gebruikersinterface met grafische alarmsignalen die operators gebruiken om het systeem te controleren en problemen op te lossen.
Bewerking volle zakken
Zodra zakken voorbij de zakkensluiter zijn, positioneert het systeem de zakken automatisch zodanig dat de voorkant van de zak naar boven is gekeerd. Dit maakt het voor klanten van Bay State Milling heel eenvoudig om bij aflevering te lezen wat de inhoud van de zak is, voor een betere klantenservice. Als de band de sluiter verlaat, draait hij 90 graden om de zakken naar een door Pemier Tech ontworpen zakkenafvlakker te sturen, die de zakken in gemakkelijk stapelbare rechthoeken perst. Vervolgens passeren de zakken een door Premier Tech ontworpen controleweegstation.
Maatwerk en gemak
Het maatwerk omvatte "het creëren van een lay-out die erg handig zou zijn voor de operators," merkt Project Manager Levesque op. "Als de transportband de vulmachine verlaat, maakt hij een bocht en loopt om de operator heen." Aangezien de controleweger automatisch elke zak met een verkeerd gewicht en elke lekkende zak weigert en dichtbij de operator plaatst, minimaliseert deze aangepaste indeling de inspanningen van de operator, waardoor de kans op letsel van de medewerker wordt verkleind.
Premier Tech leverde ook op maat gemaakte ondersteuningen voor de E55 schaal op de tweede verdieping, waardoor de vereiste technische constructie en veldconstructie van Bay State Milling werden geminimaliseerd.
De after-sales support was ook maatwerk: "We veranderden het formaat van een aantal van onze zakken nadat de installatie was voltooid en Premier Tech moest de machine herprogrammeren en opnieuw instellen om aan onze behoeften te voldoen," zegt Plant Manager Walsh.
Kleine afmetingen, grote stap voorwaarts
Om Bay State Milling te helpen direct door te kunnen werken nadat de nieuwe apparatuur was geïnstalleerd, besloten Premier Tech en Bay State Milling samen om "operators en enkele andere mensen een bezoek te laten brengen aan Premier Tech en hen de kant-en-klare machine te laten zien en 1-2 dagen training voor de machine te geven voordat hij zou worden verzonden. Op die manier raakten ze er redelijk vertrouwd mee," vertelt Project Manager Levesque.
"De PTK-2700 heeft onze productiesnelheden met 85% verhoogd ten opzichte van wat we voorheen haalden," rapporteert Plant Manager Walsh. De snelheid van de vulmachine van de fabriek bij "100-pond zakken is omhoog gegaan van 8 bpm naar 14 bpm, 50-pond zakken gingen van 10 bpm naar 19 bpm en 25-pond zakken, van 12 bpm naar 20 bpm." En hoewel het te vroeg is voor Bay State Milling om besparingen te hebben gerealiseerd op kosten van door letsel verloren arbeidstijd, merkt de heer Walsh het volgende op: "We hebben onze verpakkingsarbeid met 60% verminderd met de installatie." Ook de schoonmaakkosten zijn gedaald. "De PTK-2700 is een zeer schoon te bedienen machine en heeft onze schoonmaakwerkzaamheden verminderd. Met de installatie van de PTK-2700 hebben we een besparing gerealiseerd met een terugverdienperiode van tweeënhalf jaar voor het hele project."