Retrofit vacuümverpakker automatiseert verpakkingsproces
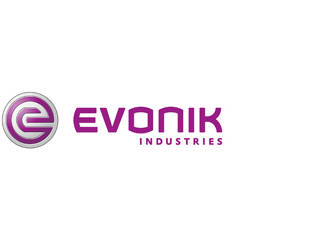
Evonik-Degussa heeft haar hoofdkantoor in Parsippany, NJ, en exploiteert een fabriek in Waterford, NY, die hydrofiel (waterabsorberend) en hydrofoob (waterafstotend) siliciumdioxide (SiO2) produceert en verpakt. Siliciumdioxide, dat als vulstof in producten zoals verven, coatings, lijmen en siliconenkit wordt gebruikt, wordt in bulk geproduceerd en wordt naar eindgebruikers verzonden in hoeveelheden die variëren van containers van 10 pond tot volle treinwagons.
Toen de fabriek in 1992 met de productie begon, werden handmatig bediende vacuümverpakkers gebruikt om papieren ventielzakken van 10 en 20 pond en 10 en 15 kilo te vullen. De handmatige verwerking van de zakken veroorzaakte echter enkele ergonomische problemen voor de operators van de fabriek. Daarom besloot het bedrijf om de verwerking van de zakken en het palletiseren te automatiseren om de ergonomie van de verpakkingslijnen te verbeteren.
Het verpakken en palletiseren van SiO2
De Waterford fabriek, onderdeel van de Inorganic Materials Division van het bedrijf, is 24 uur per dag, 7 dagen per week in bedrijf en de verpakkingslijn draait twee ploegendiensten van 12 uur per dag. Tot de fabriek voor het eerst met productie begon, was de verpakkingslijn uitgerust met twee handbediende vacuümverpakkers om de verschillende papieren ventielzakken met siliciumdioxide te vullen. Een paar jaar later nam de productie toe en de fabriek voegde een derde handmatige vacuümverpakker toe aan de verpakkingslijn. De operators moesten de zakken handmatig verwerken bij de verpakkings- en palletiseerstations.
Volgens Mark Honeyman, Aerosil Silanes NAFTA toezichthouder onderhoudstechniek, veroorzaakte het handmatig verwerken van de zakken bij de verpakkings- en palletiseerstations problemen. "Een van de grootste problemen was de ergonomie van de verpakkingslijn en onnodig tijdverlies als gevolg van ongevallen", zegt Honeyman. "Een operator die zich verrekte of een verkeerde beweging maakte bij de vacuümverpakker of het palletiseerstation was dan een tijdje uit de running. Een ander probleem betreft de nauwkeurigheid bij het vullen van de verpakkers. Aangezien hun weegsystemen niet erg nauwkeurig waren, hadden ze de neiging om vaker dan ons lief was te weinig of te veel in de zakken te doen. En omdat de verpakkingslijn een handmatige operatie was, kon hij de productielijn niet bijhouden en dat veroorzaakte een knelpunt. "Om de prestaties van de verpakkingslijn te verbeteren, nam Honeyman contact op met de leverancier van de verpakker, Premier Tech Industrial Equipment Group (IEG), om te vragen of het mogelijk was om een vacuümverpakker te voorzien van een automatisch zakverwerkings- en zaksluitsysteem. Premier Tech IEG, gevestigd in Rivière-du-Loup, Quebec, levert verpakkings-, verwerkings-, weeg-, zeef-, en sorteersystemen voor chemicaliën, farmaceutische producten, mineralen, levensmiddelen, diervoeder, bouwmaterialen en producten van andere industrieën. De leverancier had onlangs het DB-810 automatische zakverwerkingssysteem en ultrasone sluitsysteem ontwikkeld, die aan de handmatig bediende vacuümverpakker kon worden toegevoegd. De leverancier stuurde de retrofit-apparatuur naar de fabriek, en Honeyman en andere technici van de fabriek installeerden de apparatuur in oktober 2004, met steun van technici van de leverancier. "Nadat we de eerste verpakker hadden geautomatiseerd, zagen we een verbetering van de efficiëntie van de verpakkingslijn en een stijging van de productie," zegt Honeyman. "De operators hadden ook waardering voor de geautomatiseerde verpakker, omdat ze handmatig niet meer zoveel zakken als voorheen verwerkten. Toen de leverancier de verpakker van de retrofit voorzag, verbeterde hij ook het bijbehorende weegsysteem met een systeem dat veel beter presteerde dan het vorige, waardoor de nauwkeurigheid en consistentie van de zakvulling sterk verbeterde. "
Na meer dan twee jaar de voordelen te hebben gezien van een automatische verpakker besloot Honeyman dat het tijd was om de tweede handmatig bediende vacuümverpakker uit te rusten met het geautomatiseerde systeem van Premier Tech IEG . Dit keer wilde hij echter ook de palletiseeroperatie van de verpakkingslijn automatiseren om de ergonomische problemen bij het handmatig verwerken van nog meer zakken te verkleinen. Honeyman nam contact op met Premier Tech IEG en tijdens het gesprek over het nieuwe project, vernam hij dat de tweede verpakker van de fabriek kon worden uitgerust met een nieuwere versie van de DB-810 met een verbeterde functionaliteit. Evonik-Degussa keurde het verbeterde systeem goed, en in december 2006 werd de tweede verpakker uitgerust met de DB-815 met de automatische zakplaatsing en het ultrasone sluitsysteem. De palletiseeroperatie werd geautomatiseerd met de AR-200 palletiseerrobot. (Een palletiseerrobot bestaat uit een robot en alle randapparatuur — meestal transportbanden, pallet- en slipsheet-dispensers — omsloten door een veiligheidshek.) De leverancier zorgde ook dit keer voor een upgrade van het weegsysteem van de verpakker zodat de afvulling van de zakken nu nauwkeuriger geschiedt.
De geautomatiseerde vacuümverpakkers en palletiseerrobot
De DB-810 en DB-815 werken op dezelfde wijze, maar de eerste werkt pneumatisch terwijl de laatste elektromechanisch werkt. Sinds de verpakkers zijn gemoderniseerd hoeven operators bij een verpakkingsstation alleen maar lege zakken in het magazijn van de verpakker te doen: de rest van het proces is geautomatiseerd. "In het verleden moest een operator de zak van de tuit halen en het ventiel van de zak handmatig naar binnen duwen om hem te sluiten", zegt Gary Ritter, sales manager van Premier Tech IEG. "Dit leidde tot ergonomische problemen en er ontsnapte telkens een beetje stof uit de zak. De nieuwe papieren zakken hebben een extern ventiel met een plastic coating aan de binnenkant, zodat de warmte en druk die door de ultrasone sluiter wordt gegenereerd het plastic smelt en samendrukt waardoor een luchtdichte afdichting wordt gecreëerd." De AR-200 palletiseerrobot met een enkele robotarm heeft twee palletiseerstations die allebei volle zakken ontvangen van een afzonderlijke transportlijn. Een transportlijn verbindt de DB-815 direct met een palletiseerstation, en de tweede transportlijn verbindt de handmatige verpakker direct met het andere palletiseerstation. De DB-810 kan met beide palletiseerstations worden verbonden, afhankelijk van het product of de grootte van de zak die verwerkt wordt. Aangezien het bedrijf twee verschillende producten maakt en vier zakformaten gebruikt, kan de palletiseermachine zodanig worden geprogrammeerd dat er tegelijkertijd twee zakformaten worden gestapeld, ieder op zijn eigen pallet met zijn eigen stapelpatroon. Een operator hoeft alleen het zakformaat en het palletiseerstation te kiezen, en het voorgeprogrammeerde geheugen van de palletiseermachine weet vervolgens waar en in welk patroon de zakken moeten worden gestapeld.
Om het zakgewicht consistent te houden is elke transportlijn uitgerust met een controleweger die verbonden is met de palletiseermachine. Als een zak over een controleweger gaat, wordt de zak gewogen. Als het gewicht niet juist is, wordt de zak door de robotarm op een afvoerband geplaatst. Het systeem is zo geprogrammeerd dat indien de palletiseermachine geen zak ontvangt van een transportlijn, de desbetreffende verpakker stopt met het vullen van zakken. Daarnaast zijn overal in het systeem sensoren geïnstalleerd, waardoor het een failsafe systeem is, zodat de verpakkers stoppen met het vullen van zakken als er ergens in de verpakkingslijn iets misgaat. Als de palletiseermachine bijvoorbeeld geen lege pallets meer heeft, zal een sensor dit detecteren en de verpakkingslijn stopzetten omdat er geen pallets zijn waarop zakken gestapeld kunnen worden. Het bedrijf heeft slechts twee operators nodig voor het bedienen van de hele verpakkingslijn. Een operator werkt op een mezzanine. Hij houdt toezicht op de geautomatiseerde verpakkers en zorgt ervoor dat de zakmagazijnen gevuld zijn met lege zakken. De andere operator werkt op de begane grond bij de palletiseerrobot en zorgt ervoor dat de magazijnen voor pallets en slip-sheets vol zijn en voert volle pallets af van het accumulatiestation.
Verbetering van de verpakkings- en palletiseeroperaties
Sinds de modernisering van de twee vacuümverpakkers en de installatie van de palletiseerrobot is de productiviteit van het bedrijf flink toegenomen. "We verbeterden de ergonomie van de verpakkingslijn en verhoogden tegelijkertijd de productie," zegt Dr. Hauke Jacobsen, plant manager. "Nu hoeven we meestal alleen de twee geautomatiseerde verpakkers te laten draaien, omdat ze de productielijn bij kunnen houden. Daarnaast hebben we ook lang niet meer zo veel zakken die te vol zijn en zakken die niet vol genoeg zijn aangezien de geautomatiseerde verpakkers de zakken nauwkeuriger en consistenter vullen. Bovendien biedt het ultrasone sluitsysteem een stofdichte afdichting die lekkage voorkomt en de palletiseermachine stapelt de zakken op de pallets in een strak patroon dat de palletstabiliteit verhoogt. Ik ben erg blij met de oplossing die we hebben gevonden. "
Door de verpakkings- en palletiseeroperaties te automatiseren is er minder arbeid nodig bij de verpakkingslijn. Honeyman zegt er het volgende over: "De operators die bij de verpakkingslijn werken hebben nu meer tijd over om andere taken te verrichten, zoals onderhoud en inspecties, omdat ze niet meer vastzitten aan een specifieke machine of een zich voortdurend herhalende handmatige taak."