Produktivitätssteigerung dank Robotzelle
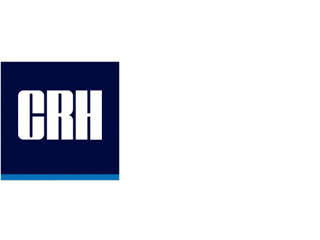
Im Werk der St. Lawrence Cement, einem Unternehmen der Holcim Group, in Catskill wurde zum Palettieren von Zementsäcken eine Palettieranlage genutzt, die nicht zuverlässig funktionierte, sodass das Unternehmen viel Zeit für die Wartung aufbringen musste, was zu massiven Ausfallzeiten führte. Außerdem bearbeitete der Palettierer sowohl Säcke als auch Paletten häufig fehlerhaft, sodass sich Kunden über gerissene Säcke und beschädigte Paletten beschwerten.
Die Maschinenführer konnten nur mit Mühe die nötige Ausbringungsmenge erreichen. Aus all diesen Gründen entschied sich das Unternehmen für den Erwerb eines neuen automatischen Palettierers. Nachdem St. Lawrence Cement im Internet, in Fachzeitschriften und anderen Quellen recherchiert hatte, standen drei Hersteller von Palettieranlagen zur Auswahl, darunter auch die Premier Tech Industrial Equipment Group (IEG). Der Vertriebsleiter der Abteilung Mineralstoffe der Premier Tech IEG, Gary Ritter, traf die Geschäftsführer, Maschinenführer und das Wartungspersonal von St. Lawrence Cement und erfasste alle für ein Angebot nötigen Informationen. Er entschied auf Grundlage dieser Informationen, dass die Anschaffung einer Robotpalettierzelle die beste Lösung wäre. „Für diese Gegebenheiten wäre sowohl ein Hochmodellpalettierer als auch eine Robotpalettierzelle in Frage gekommen“, so Ritter. „Unsere Wahl fiel auf die Robotzelle, weil sie sehr wartungsarm ist. Das Unternehmen könnte dadurch eine höhere Ausbringungsmenge unter Aufwendung von weniger Arbeitsstunden erreichen, da Ausfallzeiten reduziert und damit das Ziel der Effizienzsteigerung erreicht werden könnte.“
St. Lawrence Cement erhielt auch von den anderen beiden Herstellern Angebote. Die Entscheidung fiel aber letztendlich auf die Premier Tech IEG. „Die Wartung ist ein wichtiger Punkt, den wir schon bei der Anschaffung neuer Geräte bedenken“, so der Projektleiter. „Dabei müssen wir nicht nur berücksichtigen, ob es einfach ist, nötige Wartungsmaßnahmen durchzuführen, sondern auch, wie viele wartungsbedürftige Teile es gibt. Dieser Punkt hat bei unserer Entscheidung definitiv eine hohe Priorität. Bei dem alten Palettierer mussten mehr als fünftausend Teile gewartet werden. Die angebotene Robotzelle besitzt hingegen weniger als eintausend Wartungspunkte - eine enorme Vereinfachung. Die Entscheidung lag also auf der Hand.“
Die im Februar 2005 bestellte Robotpalettierzelle wurde im Mai desselben Jahres geliefert und installiert. Die speziell angefertigte Zelle besteht aus einem vierachsigen Roboter (FANUC), einem Palettengeber, einem Schwerkraftnebenförderband, einem Vierkantrollenförderer und einem Zubringerband. Die Maschinenführer des Unternehmens installierten das Gerät unter Aufsicht von Technikern der Premier Tech IEG. Für die Montage wurden anfänglich 15 Tage angesetzt, doch die Maschinenführer demontierten das alte Gerät innerhalb von 24 Stunden und konnten das neue Gerät innerhalb von fünf Tagen in Betrieb nehmen. Zusätzlich dauerte es zwei Tage, bis es so eingestellt war, dass es fehlerfrei funktionierte.
Seitdem gab es mit der Robotpalettierzelle keinerlei Probleme. Es waren keine größeren Reparaturen oder Ersatzteile notwendig. „Wir mussten wirklich nur kleinere Reparaturen durchführen“, so der Projektleiter. „Bei der Justierung (der Spannung) des Greifers haben wir versehentlich einen Teil des Roboterarms beschädigt. Ansonsten gab es keine Ausfallzeiten. Wir sind äußerst zufrieden mit der Anlage und auch mit dem Kundenservice.“ Dank der Robotpalettierzelle der Premier Tech IEG entfallen hohe Überstunden aufgrund des Palettierers und zusätzlich konnte die Produktivität enorm gesteigert werden. So hatten Maschinenführer im Jahr 2004 beispielsweise schon Schwierigkeiten, während einer 8-Stunden-Schicht 1.500 bis 1.700 Säcke zu palettieren. Mit der neuen Anlage sind 5.000 Säcke in derselben Zeit möglich. „Wir haben nach der Installation des neuen Geräts mit einer Steigerung von zwanzig Prozent gerechnet“, so die Geschäftsführer. „Tatsächlich waren es mehr als fünfunddreißig Prozent. Unsere Kunden sind mit der gesteigerten Ausbringungsmenge und auch mit dem Endprodukt sehr zufrieden. Das Projekt war für uns ein großer Erfolg.“