Automatisierung des Verpackungsvorganges durch eine automatische Absackanlage und eine Robotpalettierzelle
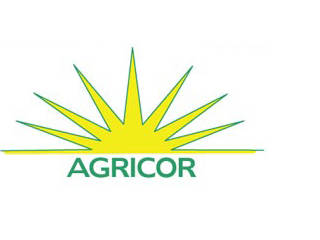
Eine Maismühle automatisiert den Absack- und Palettiervorgang, steigert so die Ausbringungsmenge und senkt die Arbeitskosten. Seit 1983 produziert Agricor Inc. mit Sitz in Marion, Indiana, USA, trocken gemahlene Maisprodukte. Das Unternehmen kauft gelben Mais von lokalen Landwirten und Getreidesilos auf und mahlt diesen zu keimfreiem Maisgrieß und Maismehl. Die Produkte werden in Schüttgutbehältern wie Schüttgutsäcken und Schüttgutwagen oder 50- und 100-Pfund Säcken verpackt und an Unternehmen im In- und Ausland geliefert, wo sie bei der Herstellung von Nahrungsmitteln und Industrieprodukten weiterverarbeitet werden. In der Vergangenheit wurden kleine Säcke manuell befüllt und palettiert, was jedoch ineffizient und arbeitsintensiv war und zu Staubaufwirbelungen führte. Das Unternehmen entschied sich daher für eine Automatisierung.
Unterschiedlichste Anforderungen an die Verpackungen
Jährlich werden bei Agricor Inc. mehr als 130.000 Tonnen Mais zu Maisgrieß und Maismehl gemahlen. Aufgrund von Abweichungen bei der Produktdichte und dem Volumen der verschiedenen Produkte, verwendet das Unternehmen beim Absacken drei unterschiedliche Größen bei den 100-Pfund-Säcken und zwei unterschiedliche Größen bei den 50-Pfund-Säcken.
Schwierigkeiten beim Absacken und Palettieren
Für das manuelle Absacken und Palettieren waren, je nach Größe der abzufüllenden Säcke, vier bis sechs Mitarbeiter pro Schicht nötig. Ein Mitarbeiter zog die befüllten Säcke durch ein Verschweißgerät, ein bis drei Mitarbeiter stapelten die vollen Säcke auf Paletten, ein Mitarbeiter beseitigte Produktverschüttungen und Staub und füllte das Sackmagazin wieder auf und ein Mitarbeiter transportierte die vollen Paletten mit dem Gabelstapler ins Lager.
Beim manuellen Absacken und Palettieren der verschiedenen Produkte erreichte das Unternehmen sowohl bei 100-Pfund-Standardsäcken als auch bei 100-Pfund-Maismehlsäcken eine Leistung von 5 Säcken pro Minute, bei 100-Pfund-Mehlsäcken eine Leistung von 3 Säcken pro Minute, bei 50-Pfund-Standardsäcken eine Leistung von 7 Säcken pro Minute und bei 50-Pfund-Mehlsäcken eine Leistung von 4 Säcken pro Minute. Um diese Rate jedoch aufrecht erhalten und die Nachfrage weiter bedienen zu können, musste das Unternehmen bei einer Sechs-Tage-Woche in drei Schichten pro Tag produzieren und in jeder Schicht bis zu zwei Zeitarbeitskräfte beschäftigen.
„Wir konnten die Probleme bei der Produktion nur durch mehr Mitarbeiter lösen", so Jack Jones, Lager- und Verpackungsleiter bei Agricor. „Ein Mitarbeiter half mit dem Gabelstapler beim Stapeln der Paletten mit 100-Pfund-Säcken. Zwei Mitarbeiter stapelten die 50-Pfund-Säcke manuell und in Zeiten, in denen wir mehr verpacken mussten, benötigten wir drei Mitarbeiter. Um die Risiken zu minimieren, die bei der manuellen Verarbeitung so vieler Säcke entstehen können, wechselten sich die Mitarbeiter in jeder Schicht an den Absackungs- und Palettierstationen ab. Rückblickend können wir froh sein, dass beim manuellen Absacken und Palettieren so vieler Säcke keine Ergonomieprobleme entstanden sind, was für uns stets ein kritischer Punkt war."
Steve Wickes, Geschäftsführer von Agricor, berichtet von einem weiteren Problem: „Bei der Füllgenauigkeit waren starke Schwankungen zu verzeichnen. Das Gewicht der Maisgrieß- und Maismehlsäcke wich bis zu einem Pfund von den Vorgaben ab. Bei den Mehlsäcken waren die Schwankungen sogar noch größer. Und da wir uns im Zweifel immer für eine Überfüllung der Säcke entschieden, kam es bei nahezu jeder Absackung zu Produktverlusten, was sich negativ auf unsere Gewinnspanne auswirkte."
Der Absackungs- und Palettiervorgang musste also dringend optimiert werden, vor allem da das Unternehmen seinen Kundenstamm weiter ausbauen wollte. „Eine Erhöhung der Produktionsrate war nicht möglich, da die Verpackungsstation bereits die maximale Auslastung erreicht hatte. Folglich stagnierte die Produktion", so Wickes. „Außerdem mussten wir eine bessere Füllgenauigkeit erreichen, um den Produktverlust so gering wie möglich zu halten, die Anzahl der Mitarbeiter an den einzelnen Stationen zu verringern sowie die Absack- und Palettierdauer zu verkürzen. Also entschieden wir uns für eine Vollautomatisierung des Verpackungsvorgangs und für eine Aufrüstung der Metalldetektoren, um eine höhere Produktreinheit zu gewährleisten."
Suche nach Automatisierungslösungen
Wickes und Jones setzten sich mit einer Reihe von Herstellern für Absack- und Palettieranlagen in Verbindung. „Wir erklärten, dass wir auf der Suche nach einem automatischen Absackanlage, einer Verschweißanlage und einer Robotpalettierer sind, die eine Verarbeitung aller drei Produkte ohne die zeitraubende Neueinstellung zwischen jedem Durchlauf ermöglicht", so Jones. „Außerdem machten wir deutlich, dass für die Verpackungsanlage nur wenig Platz zur Verfügung steht und dass für das Förderband und die gesamte Anlage aus Platzgründen möglicherweise eine Sonderanfertigung erforderlich wäre. Zusätzlich musste der Abbau der alten und die Montage der neuen Anlage in relativ kurzer Zeit erfolgen, da wir unseren Produktionsplan einhalten mussten. Dem Hersteller standen deshalb effektiv gerade einmal zwei Wochenenden bzw. ca. 96 Stunden zur Verfügung, um die gesamte Verpackungsanlage zu montieren.“
Beim Vergleich der Angebote und der einzelnen Punkte fiel Wickes und Jones vor allem ein Angebot auf. „Wir verglichen die Installationskosten, die Preise der Anlagen sowie deren Qualität und Aufbau, das jeweilige Projektmanagement und den Kundendienst und kamen zu dem Schluss, dass für unsere Anforderungen und unser Budget nur ein Hersteller in Frage kommt", so Wickes. „Bevor wir eine endgültige Entscheidung trafen, schickten wir dem Hersteller unsere Produkte für einen Durchlauf in der Testanlage und sahen uns eine Anlage in Toronto an. Außerdem sprachen wir mit einem ihrer Kunden in Saskatchewan. Bei dem Testdurchlauf stellte sich heraus, dass die Absackanlage des Herstellers unsere drei Produkte problemlos verarbeiten konnte und wir erhielten ausnahmslos positive Rückmeldungen der anderen Kunden des Herstellers. Also entschlossen wir uns zum Kauf einer automatischen Absackanlage für Offensäcke mit automatischer Sackverschweißung und einer programmierbaren Robotpalettierzelle des Herstellers.
Der Hersteller, Premier Tech Industrial Equipment Group (IEG) mit Sitz in Rivière-du-Loup, Quebec, Kanada, ist auf die Konzeption und Fertigung von maßgeschneiderten und automatisierten Verpackungsanlagen, Palettieranlagen, Systemen zur Dosierung, Stretchwicklern sowie Trockenschüttgutanlagen spezialisiert.
Automatische Absackanlage und Robotpalettierzelle
Mit der Hochleistungs-Absackanlage PTK 1700 können Pulver und Granulate - darunter Mineralien, Chemikalien, Nahrungsmittel und Tierfutter - in Papier-, PE- und gewebte PP-Offensäcke abgesackt werden. Je nach Sackmaterial und Größe kann dabei eine Leistung von bis zu 25 Säcken pro Minute erreicht werden. Bei der Absackanlage kommen nur Edelstahlteile mit den Produkten in Kontakt. Sie ermöglicht ein staubfreies Absacken, bei dem die vollständige Kontrolle während des gesamten Verschließprozesses gewährleistet bleibt. Sie erfüllt somit die Anforderungen für den hygienegerechten Einsatz in der Lebensmittelproduktion. Außerdem werden die befüllten Säcke schnell und zuverlässig zur automatischen Verschweißanlage befördert.
Die PLC-gesteuerte Absackanlage verfügt über einen anwenderfreundlichen Touchscreen zur einfachen Fehlerauslesung und -behebung. Die Selbstdiagnose-Software mit Not-Aus-Schalter gewährleistet die Bedienersicherheit während des Betriebs. Dank der integrierten Wägesteuerung wird das Materialgewicht laufend präzise erfasst. Das Sackmagazin für mehrere Sackstapel ermöglicht ein schnelles Nachladen und Wechseln der Sackgrößen.
Die Robotpalettierzelle AR-200 nimmt mehrere Säcke von bis zu vier verschiedenen Produktionsanlagen gleichzeitig auf und palettiert, abhängig von Sackart, Palettenhöhe, Gerätekonfiguration und weiteren Faktoren, bis zu 28 Säcke pro Minute. Für den Einsatz bei Agricor wurde die Palettierzelle aufgrund des Platzmangels so konfiguriert, dass nur Säcke von einer Produktionsanlage aufgenommen werden.
Die Robotersteuerung verfügt über eine anwenderfreundliche, PLC-gesteuerte Bedienoberfläche auf der dreidimensionale Anlagen- und Aufbaupläne für eine einfache Bedienung im manuellen Betrieb angezeigt werden Die Bedienoberfläche zeigt auch gespeicherte Vorlagen an, auf die der Bediener zur Änderung der Sackgröße und der Palettiermuster zugreifen kann.
Der vollautomatische Palettierer nimmt leere Paletten und die Zwischenlagen automatisch auf und der Roboterarm ist mit einem Fingergreifer ausgestattet, mit dem Abweichungen in der Produktdichte ausgeglichen werden können. So können problemlos Säcke mit einer Breite von 23 bis 58 cm, einer Länge von 33 bis 100 cm, einer Dicke von 4 bis 15 cm und einem Gewicht von bis zu 176 Pfund verarbeitet werden. Das PLC-System des Palettierers verfügt über eine Software zur Kollisionsüberwachung, um Beschädigungen am Greifer des Roboterarms und an anderen Teilen zu verhindern.
Installation der Verpackungsanlage
Das Unternehmen beauftragte einen örtlichen Mühlenbauer (Industrial Maintenance Specialists) und eine Elektroinstallationsfirma (Rex Collins Electric) mit der Installation der neuen Anlage. Am Freitag, dem 15. Februar 2008, begannen der Mühlenbauer und die Ingenieure des Herstellers sowie die Mitarbeiter von Agricor nachts mit dem Abbau der alten Absackanlage. „Wir bauten die alte Absackanlage ab und stellten die neue auf", so Jones „und am darauffolgenden Wochenende installierten wird die Robotpalettierzelle, die Förderbänder und alle übrigen Teile. An beiden Wochenenden konnten wir unseren straffen Zeitplan einhalten, sodass wir die Absackung bereits am Sonntagabend wieder aufnehmen konnten. Das war schon eine beeindruckende Leistung, denn schließlich durften wir uns wegen des begrenzten Platzes keine Ungenauigkeiten beim Aufbau erlauben. Zwischen der Anlage und der Wand sind gerade einmal 8 cm Abstand. Das zeigt, wie kompakt die gesamte Anlage ist."
Nun werden nur noch drei Mitarbeiter pro Schicht für den Betrieb der Verpackungsanlage benötigt: Einer für die Überwachung der gesamten Anlage, einer für die Reinigung und einer, der den Gabelstapler fährt. Zurzeit beträgt die Absackleistung für 100-Pfund-Standardsäcke und 100-Pfund-Maismehlsäcke zwischen 9 und 11 Säcke pro Minute, für 100-Pfund-Mehlsäcke zwischen 7 und 9 Säcke pro Minute, für 50-Pfund-Standardsäcke 15 Säcke pro Minute und für 50-Pfund-Mehlsäcke zwischen 8 und 10 Säcke pro Minute.
Optimierung des Verpackungsvorgangs
Seit die neue Verpackungsanlage in Betrieb ist, konnte das Unternehmen seine Betriebs- und Arbeitskosten bereits erheblich senken. „Die Absackung läuft so schnell, dass wir nur noch an fünf Tagen in der Woche in zwei Schichten pro Tag arbeiten müssen, um unseren Produktionsplan einhalten zu können", so Wickes. „Und dank der Robotpalettierzelle konnten wir die Arbeitskosten senken, da wir in Phasen des Hochbetriebs keine Zeitarbeitskräfte zum Palettieren der 50 Pfund-Säcke mehr einstellen müssen. Auch müssen wir nun keine Ergonomieprobleme in Folge der manuellen Verarbeitung so vieler Säcke mehr befürchten."
Dank der hohen Wägegenauigkeit der Absackanlage und der daraus resultierenden Verminderung des Produktverlustes hat sich die Gewinnspanne des Unternehmens erhöht. „Wir sind sehr zufrieden", so Jones. „Es gibt nur äußerst minimale Abweichungen bei der Wägegenauigkeit und unsere Kunden sind dankbar, dass sie genau die Produktmenge erhalten, die sie auch bestellt haben."
Sowohl Wickes als auch Jones waren sehr zufrieden mit der herstellerseitigen Bedienerschulung und dem Kundenservice nach der Installation. „Die Ingenieure der IEG haben unsere Mitarbeiter hervorragend geschult und ihnen verdanken wir, dass wir in so kurzer Zeit die Produktion wieder aufnehmen konnten", so Wickes. „Auch wenn die Technologie für uns relativ neu ist und wir deshalb viel dazu lernen mussten, machen wir täglich Fortschritte in der Bedienung der Anlagen. Die Zusammenarbeit mit der IEG war äußerst angenehm und wir hatten stets Ansprechpartner, die sich unverzüglich um Probleme kümmerten. Der große Vorteil ist, dass der Kundendienst der IEG bis zehn Uhr abends erreichbar ist, sodass wir sofort telefonische Hilfe erhalten."
Überarbeiteter Artikel aus dem Powder & Bulk Engineering Magazine, März 2009.