Fallbeispiel Moulin Peterschmitt: Auf Dem Neuesten Stand Der Technik Bleiben
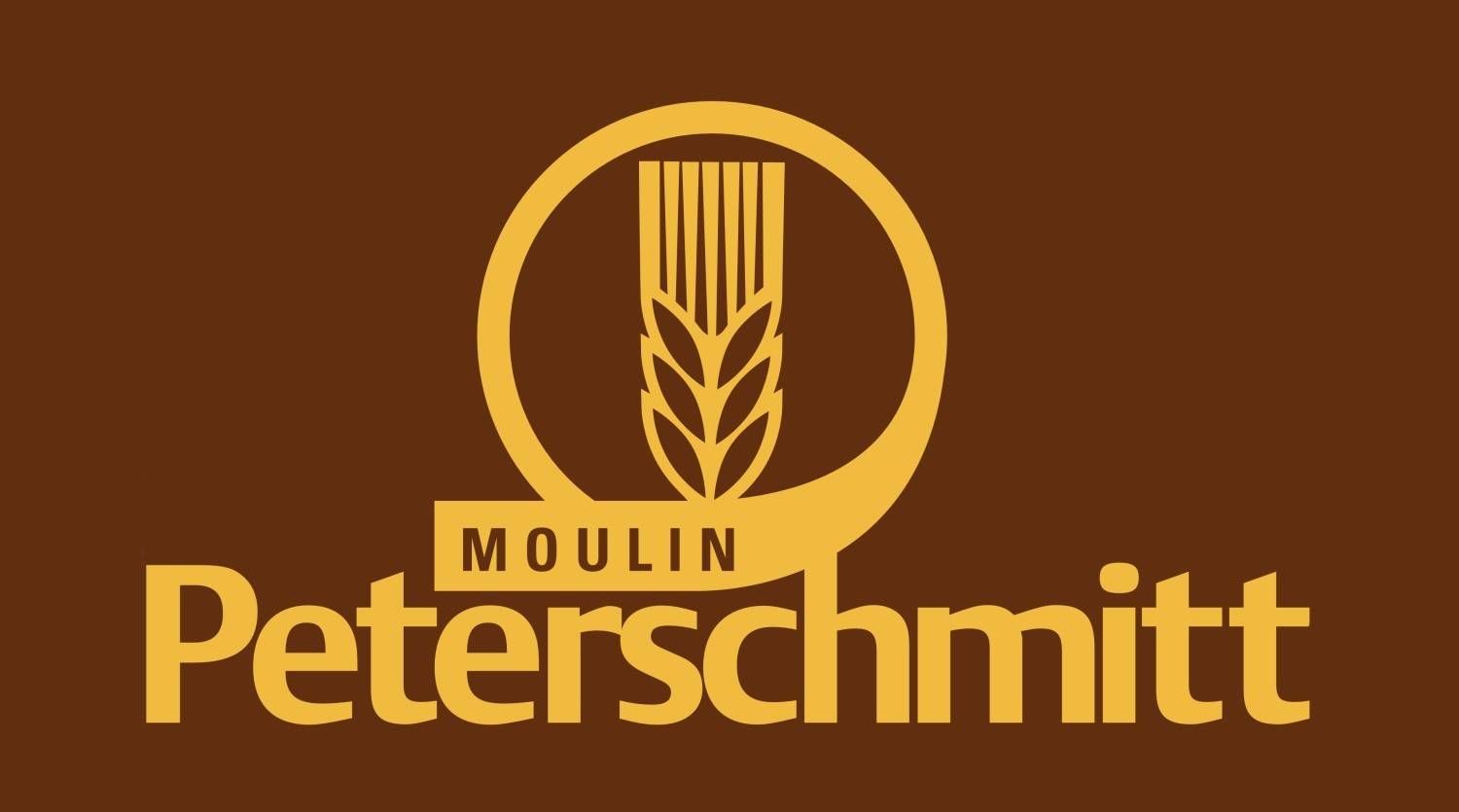
UNTERNEHMENSPROFIL
Moulin Peterschmitt ist eine Getreidemühle im Elsass in Frankreich. Die Mühle wurde 1782 gegründet und ist seit Generationen im Besitz der Familie Peterschmitt. Marc Peterschmitt, der Geschäftsführer, übernahm den Betrieb vor einigen Jahren von seinem Vater und betreibt die Mühle zusammen mit seinen Brüdern Luc und Daniel. Sie leiten die Mühle bereits in siebter Generation.
Moulin Peterschmitt produziert Weichweizenmehl und hat einen großen Kundenstamm, der von Privatpersonen bis hin zu Industrieunternehmen reicht. Die Mühle vertreibt das Mehl daher in den verschiedensten Gebinden, von 1-kg-Säcken bis hin zu Lastwagen, die 30 Tonnen Schüttgut befördern.
IN DER MEHLINDUSTRIE WETTBEWERBSFÄHIG BLEIBEN
Moulin Peterschmitt ist ständig bestrebt, seine Anlagen zu modernisieren, um deren Wettbewerbsfähigkeit in einem ohnehin hart umkämpften Markt aufrechtzuerhalten. 1782 verfügte das Unternehmen über eine Mühle, die pro Tag rund 500 kg Weizen mahlte. Mittlerweile produziert das Unternehmen 5 Tonnen Weizenmehl pro Stunde.
Das reicht aber nicht aus, um konkurrenzfähig zu bleiben: Die Mühle wollte größere Mengen produzieren. Darüber hinaus sollten die neuen Anlagen die Hygiene verbessern, den Automatisierungsgrad erhöhen und neue Absatzmöglichkeiten für Moulin Peterschmitt eröffnen.
ETAILPLANUNG FÜR NEUE ANLAGEN
Die Erhöhung der Produktionskapazität war der erste Schritt in diesem Plan, und Marc Peterschmitt und seine Brüder hatten ein klares Ziel vor Augen: die Verdopplung der Produktion auf 10 Tonnen pro Stunde mit Option auf eine weitere Erhöhung.
Zur Verbesserung der Hygiene fanden sie zwei Maschinen auf dem Markt, die Säcke nach dem Botton-Up-Prinzip mit sehr geringer Staubentwicklung befüllen und daher zur Aufrechterhaltung der Anlagensauberkeit beitragen. Eine Maschine war von Premier Tech, die andere von einem Wettbewerber.
Die Absackanlage musste außerdem automatisiert werden: „Sie musste in der Lage sein, mindestens 5 bis 6 Paletten selbstständig ohne Eingriff eines Dritten im Voraus vorzubereiten. Für uns kam es nicht in Frage, ständig einen Mitarbeiter in unmittelbarer Nähe der Maschine zu haben, der sicherstellt, dass alles ordnungsgemäß funktioniert“, so Peterschmitt.
Mit der alten Absack- und Palettieranlage war die Mühle nicht in der Lage, eine entscheidende Vertriebsmöglichkeit wahrzunehmen: die Teilnahme an Ausschreibungen für befüllte Säcke. Damit blieb das Unternehmen in diesem Teil des Marktes außen vor.
WAHL FÄLLT AUF PREMIER TECH
Zu Zeiten von Marc Peterschmitts Großvater besaß das Unternehmen eine Waage von Richardson Chronos, mit der der Weizen direkt bei der Anlieferung durch die Landwirte gewogen wurde. Das Unternehmen stieg dann vor 12 Jahren auf eine teilautomatisierte Anlage um. „Diese Maschine hatte ausgedient“, so Peterschmitt, und es war Zeit für ein neues Modell.
Peterschmitt wurde sofort, nachdem er sein Interesse an einer Absackanlage zum Ausdruck gebracht hatte, an ein Mitglied des Verkaufsteams weitergeleitet. „Und dieser Mitarbeiter war sehr engagiert und hat immer alle unsere Fragen beantwortet, geduldig zugehört und mir die verschiedenen Möglichkeiten aufgezeigt, die für uns in Frage kamen“, erzählt Peterschmitt.
Darüber hinaus konnten er und sein Team eng mit dem Konstruktionsteam der verschiedenen an dem Projekt beteiligten Firmen zusammenarbeiten, darunter nicht nur Premier Tech, sondern auch die Hersteller der Silos und das für den Umbau des Gebäudes ausgewählte Unternehmen.
Letztendlich entschied sich Moulin Peterschmitt nicht nur für eine Absackanlage, sondern auch für einen Lagenpalettierer für Säcke, da die Paletten per LKW transportiert werden mussten und zur effizienten Beladung der LKWs die strikte Einhaltung der Längen- und Breitenmaße erforderlich war.
DER ERSEHNTE WETTBEWERBSVORSPRUNG
Moulin Peterschmitt ist ein Unternehmen mit einer jahrhundertealten Tradition, das seiner Zeit voraus bleiben möchte. Die Modernisierung eines Teils der Anlage verdoppelte die Produktionskapazität, verbesserte die Hygiene, ermöglichte die Automatisierung und öffnete die Türen für neue Geschäfte. „Ich denke, wir haben definitiv die richtige Wahl getroffen“, so Peterschmitt.