Cómo desmitificar los empaquetadores de bolsas de válvula
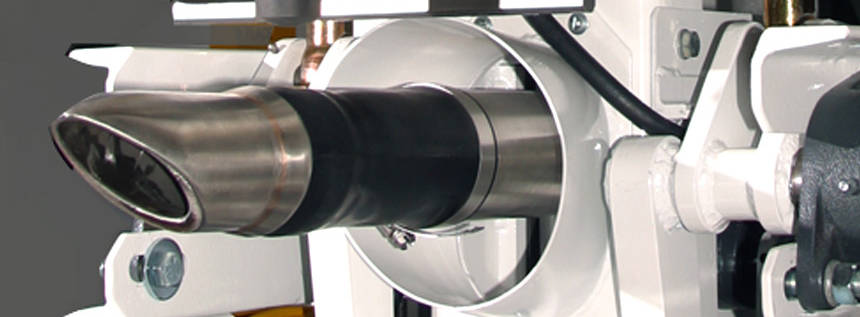
Al final del siglo XX, Adelmer M. Bates, un vendedor de sal, inventó la bolsa de válvula. La historia cuenta que él estaba vendiendo más sal de lo que su empresa podía distribuir y el método de llenado que se empleaba en esos días parecía limitar las comisiones de las ventas. En cuanto el Sr. Bates desarrolló la bolsa, comenzó una nueva y arriesgada empresa para desarrollar el equipo que le permitiera llenar su nueva bolsa. Desde entonces, cinco máquinas han evolucionado para manipular la amplia gama de productos que llenan las bolsas de válvula:
- El empaquetador de aire (también llamado de flujo forzado).
- El empaquetador de barrena.
- El empaquetador de gravedad.
- El empaquetador impulsor (también llamado de chorro).
- El empaquetador de vacío.
Aunque las bolsas de válvula se pueden llenar efectivamente con muchos productos granulados o en pellets, el mayor uso que se le ha dado a las bolsas de válvula se ha centrado en los productos en polvo o en las mezclas que incluyen polvos. Como la abertura de la bolsa de válvula es mucho más pequeña que la de una bolsa de boca abierta, se puede controlar mejor el flujo del producto en polvo.
La primera ventaja de las bolsas de válvula fue que tenían cierre automático y reducían la mano de obra requerida para llenarlas y sellarlas a diferencia de los sacos de boca abierta de aquellos tiempos (cosidos a mano). A pesar de muchas innovaciones realizadas en el diseño de la válvula, las que incluyen cierre de película y de doble trampa, el cierre automático dista mucho de ser un sello hermético. Por esta razón, muchas de las bolsas que se usan en la industria de productos químicos y de alimentos se sellan ultrasónicamente después del llenado. Otra ventaja de las bolsas de válvula es que se llenan de manera más ajustada y tienen una forma más cuadrada, lo que hace que se apilen mejor en la bandeja de carga (en comparación a otras formas de bolsa como las de boca abierta y las que se usan para formación, llenado y sellado).
La bolsa de válvula original del Sr. Bates era de género. La inmensa mayoría de las bolsas de válvula hoy se fabrican de múltiples pliegues de papel con un pliegue de polietileno opcional. Aunque las bolsas de válvula se pueden hacer de polietileno o de polipropileno tejido, la mayoría se fabrica de papel.
De los cinco tipos de equipo mencionados anteriormente, cuatro se usan en forma regular. El empaquetador de gravedad se usa rara vez, ya que funciona mejor con productos granulados o en pellets y estos productos se pueden llenar mejor en bolsas de boca abierta o en el equipo de formación, llenado y sellado. Hay mucha superposición en las aplicaciones de estas máquinas.
Para ayudarle a tomar una decisión, a continuación se discuten los pros y los contras de las cuatro máquinas restantes:
Empaquetador de aire (de flujo forzado)
Pros:
- Llenado rápido.
- Buena precisión.
- Versátil: funciona con polvo fino y con productos de partículas que miden hasta 9,5 mm (3/8”).
- No tiene piezas móviles en el flujo del producto.
- Suave manipulación del producto: no hay deslizamientos mecánicos, degradación mínima.
- Fácil de limpiar: se puede acceder al fondo de caída y la cámara.
Contras:
- Le agrega aire al producto durante el llenado.
- Riesgo de que se reviente una bolsa, ya que se llenan a presión.
- No manipula bien los productos muy livianos (< 160 kg/m³ [< 10 lb/ft³]).
- No manipula bien los productos “pegajosos” (como las mezclas de panadería con contenido de grasa).
Empaquetador de barrena
Pros:
- Le agrega poco aire al producto durante el llenado.
- Rara vez se revienta una bolsa, ya que no se llenan a presión.
- Pocos ajustes: método de llenado mecánico fácil de entender.
- Versátil: manipulará una amplia gama de productos, entre los que se incluyen productos “pegajosos” difíciles como las mezclas de panadería con contenido de grasa.
Contras:
- Es posible que requiera un asentamiento violento para llenar ajustadamente una bolsa.
- Los polvos fluidificados pueden inundar la barrena, aún cuando esta esté detenida.
- Generalmente es más lento que otros métodos de llenado.
- Pocas maneras de programar la máquina con los ajustes ideales para múltiples productos.
- Sujeto a la abrasión: los componentes de desgaste están en el flujo del producto.
- Puede provocar deslizamiento mecánico y degradación del producto.
Empaquetador impulsor (de chorro)
Pros:
- Llenado rápido de la mayoría de los polvos.
- Bolsas que se llenan en forma ajustada.
Contras:
- Tamaño de productos limitado: tamaño de malla de 200 o partículas más finas.
- Dificultad para limpiar (antes del cambio rápido de un producto).
- Sujeto a la abrasión: los componentes de desgaste están en el flujo del producto.
- Puede provocar deslizamiento mecánico y degradación del producto.
- Le agrega aire al producto durante el llenado.
- Riesgo de que se reviente una bolsa, ya que se llenan a presión.
- Algunos productos pueden provocar calor en la caja del impulsor: es posible que el producto se chamusque.
Empaquetador de vacío
Pros:
- Manipula bien los productos muy livianos (< 160 kg/m³ [< 10 lb/ft³]).
- Produce bolsas que se llenan en forma ajustada.
- Suave manipulación del producto: no hay deslizamientos mecánicos, degradación mínima.
- No tiene piezas móviles en el flujo del producto.
- Si una bolsa explota durante el llenado, el producto es contenido en una cámara de vacío, el ambiente permanece limpio.
Contras:
- Dificultad para llenar una bolsa que tiene pliegues de barrera de polietileno.
- Llenado lento.
- Es costoso comparado con otros métodos de llenado.
- Las bolsas pueden explotar durante el llenado.
En general, los empaquetadores de aire y de barrena se usan para alimentos, productos químicos, minerales y algunos tipos de alimentación. Los empaquetadores impulsores se usan principalmente para minerales, mientras que los de vacío se usan principalmente para productos químicos. Aunque es sensato considerar primero las máquinas que se usan tradicionalmente para sus productos, es posible que también quiera considerar los beneficios únicos de un tipo de máquina específica. La mayoría de los fabricantes de equipos ofrecen servicios de prueba para ayudarle a decidir cuál máquina es mejor para su producto y sus necesidades.